§ 1. Метады апрацоўкі металаў рэзаннем
Пераважны лік дэталей машын набываюць форму і памеры толькі пасля механічнай апрацоўкі - апрацоўкі металаў рэзаннем. Да апрацоўкі будучая дэталь называецца нарыхтоўкай. Каб атрымаць неабходную дэталь, з загатоўкі трэба зняць частку металу, якая называецца прыпускам. Працэс зняцця прыпуску рэжучай прыладай з мэтай атрымання дэталі зададзенай формы, памераў і дакладнасці завецца рэзаннем.
Для ажыццяўлення працэсу рэзання нарыхтоўцы і прыладзе неабходна паведаміць вызначаны комплекс рухаў. Гэтыя рухі можна падзяліць на асноўныя (для ажыццяўлення працэсу рэзання) і дапаможныя (для падрыхтоўкі да працэсу рэзання і завяршэнні аперацыі). Асноўныя рухі два: галоўны рух - рух рэзання і рух падачы.
Галоўны рухнепасрэдна дазваляе ажыццяўляць працэс рэзання (адукацыі стружкі), рух падачы дае магчымасць весці працэс зняцця стружкі з усёй апрацоўванай паверхні.
У залежнасці ад характару выкананых прац і выгляду рэжучай прылады адрозніваюць наступныя метады апрацоўкі металаў рэзаннем: тачэнне, свідраванне, шліфаванне, фрэзераванне, габлёўка, працягванне і інш. На мал. 1 прыведзены схемы розных метадаў апрацоўкі металаў рэзаннем.
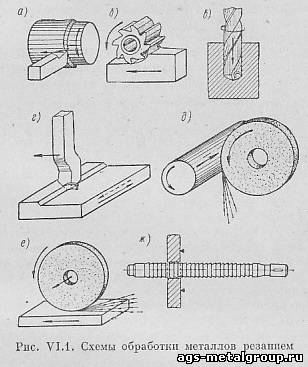
Пры тачэнні загатоўцы паведамляецца вярчальны галоўны рух, а інструменту рух падачы (мал. 1, а).
Пры фрэзераванні галоўны (круцільны) рух паведамляецца прыладзе (фрэзе), а рух падачы - нарыхтоўцы (мал. 1, бы).
Пры свідраванні як галоўны (круцільны) рух, так і рух падачы звычайна паведамляецца прыладзе (мал. 1, у).
Пры габлёўцы на падоўжна-стругальных станках галоўны (зваротна-паступальны) рух паведамляецца нарыхтоўцы, а рух падачы - прыладзе (мал. 1, г).
Пры габлёўцы на папярочна-стругальных станках і пры апрацоўцы на долбежных станках галоўны рух паведамляецца прыладзе, а рух падачы - нарыхтоўцы.
Пры шліфаваннігалоўны рух заўсёды круцільны, ён ажыццяўляецца прыладай (шліфавальным кругам). Пры круглым шліфаванні (мал. 1, д) адначасова круціцца і нарыхтоўка, чым забяспечваецца кругавая падача. Бо ў большасці выпадкаў даўжыня якая шліфуецца дэталі больш шырыні круга, апыняецца неабходнай яшчэ і падоўжная падача (уздоўж восі нарыхтоўкі), якая ажыццяўляецца нарыхтоўкай або кругам. Прымяняецца таксама радыяльная падача, якая забяспечвае паступовае зняцце прыпуску на ўсю глыбіню.
Пры плоскім шліфаванні падоўжная падача ажыццяўляецца часцей за ўсё нарыхтоўкай, а папярочная падача - шліфавальным кругам або нарыхтоўкай. (мал. 1, е).
Пры працягваннігалоўны рух прамалінейны і паведамляецца прыладзе (протяжке), а паступовае зняцце стружкі (падача) забяспечваецца рознасцю вышынь кожных двух сумежных зуб'яў протяжки (мал. 1, ж).
§ 2. Геаметрыя разцоў
Схема апрацоўкі дэталі тачэннем і ўзаемнае размяшчэнне апрацоўванай дэталі і інструмента прыведзены на мал. 2, а. На дэталі падчас рэзанні адрозніваюць апрацоўваную і апрацаваную паверхні і паверхня рэзання.
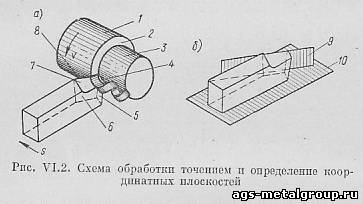
Апрацоўваная паверхня 1 - гэта паверхня нарыхтоўкі на тым яе ўчастку, які маецца быць апрацаваць на дадзенай аперацыі; апрацаваная паверхня 3 - паверхня, якая атрымліваецца пасля аддзялення зразальнага пласта, т. е. пасля апрацоўкі; паверхня рэзання 2 - паверхня, якая ўтвараецца на апрацоўванай дэталі, рэжучай абзой разца.
Прынцып працы любой рэжучай прылады заснаваны на дзеянні кліну. Працоўную частку разца, якая здзяйсняе рэзанне, абмяжоўваюць: перадпакой паверхня 7, па якой сыходзіць якая ўтвараецца падчас рэзанні стружкі; галоўная задняя паверхня 6 разца, звернутая да паверхні рэзання; дапаможная задняя паверхня 5 - паверхня разца, звернутая да апрацаванай паверхні дэталі.
Галоўная рэжучая абза 8 утворыцца скрыжаваннем перадпакоя і галоўнай задняй паверхняў. Дапаможны рэжучы беражок 4 утворыцца скрыжаваннем перадпакоя і дапаможнай задняй паверхняў. Кропка скрыжавання галоўнай і дапаможнай рэжучых беражкоў завецца вяршыняй разца.
Узаемнае размяшчэнне паверхняў разца, а таксама іх размяшчэнне адносна апрацоўванай дэталі вызначаюцца групай кутоў. Для вызначэння вуглоў, якія характарызуюць геаметрыю разца, уводзіцца паняцце аб каардынатных плоскасцях: плоскасці рэзання і асноўнай плоскасці (мал. 2, б).
Плоскасць рэзання 9 датычная да паверхні рэзання і праходзіць праз галоўны рэжучы беражок. Асноўная плоскасць 10 паралельная напрамкам падоўжнай і папярочнай падач. У разцоў з прызматычным целам гэтая плоскасць супадае з ніжняй апорнай паверхняй разца.
Вуглы разца вымяраюцца ў галоўнай сякучай плоскасці, перпендыкулярнай да праекцыі галоўнай рэжучай абзы на асноўную плоскасць (мал. 3, а). Галоўным заднім вуглом α называецца вугал, утвораны галоўнай задняй паверхняй інструмента і плоскасцю рэзання. Гэты кут неабходзен для памяншэння трэння паміж апрацоўванай дэталлю і разцом. Практычна вугал α прымаецца ў межах 6 - 12˚.
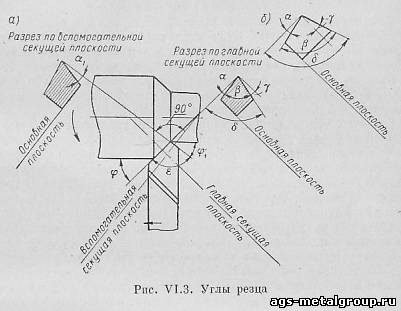
Пярэднім вуглом γ называецца вугал паміж пярэдняй паверхняй і нармаллю да плоскасці рэзання. Велічыня пярэдняга кута аказвае істотны ўплыў на працэс стружкаўтварэння. Велічыня кута γ вагаецца ў шырокіх межах - ад +25 да - 10˚.
Кут завастрэння β - гэта кут паміж пярэдняй і галоўнай задняй паверхнямі. Чым ён больш, тым трывалей рэжучая частка прылады і тым лепш умовы адводу цяпла ад рэжучага ляза.
Вуглам рэзання δ называецца вугал паміж пярэдняй паверхняй і плоскасцю рэзання.
З мал. 3 відавочна, што α + β + γ = 90˚; δ = α + β = 90˚ - γ.
Калі вугал δ < 90 (мал. 3, а), то вугал γ мае дадатнае значэнне. Пры δ> 90' (мал. 3, б) вугал γ набывае адмоўнае значэнне.
Пры дадатным значэнні γ палягчаюцца ўмовы сходу стружкі, але затое памяншаецца трываласць рэжучага кліну, пагаршаюцца ўмовы адводу цяпла ад рэжучага кліну. Акрамя таго, дзеянне сілы рэзання, накіраванае па нармалі да пярэдняй паверхні, выклікае ў рэжучым кліне дэфармацыі выгібу і зрэзу.
Пры адмоўным значэнні кута γ трываласць кліну павялічваецца, паляпшаюцца ўмовы адводу цяпла, а сілы рэзання выклікаюць толькі дэфармацыі сціску, якія добра вытрымліваюцца як прыладамі са сталі, так і з цвёрдых сплаваў. Аднак у гэтым выпадку ўмовы сходу стружкі значна пагаршаюцца, а такім чынам, павялічваецца магутнасць, якая затрачваецца на рэзанне.
Дапаможны задні вугал α₁ вымяраецца ў дапаможнай сякучай плоскасці. Гэты вугал неабходны для памяншэння трэння па дапаможнай задняй паверхні і прымаецца ў большасці выпадкаў роўным галоўнаму задняму вуглу α.
Важнае значэнне падчас рэзанняў маюць куты ў плане. Адрозніваюць галоўны і дапаможны куты ў плане. Вуглы ў плане вымяраюцца ў асноўнай плоскасці (мал. 3, а).
Галоўным вуглом у плане φ называецца вугал паміж праекцыяй галоўнай рэжучай абзы на асноўную плоскасць і напрамкам падоўжнай падачы. У залежнасці ад умоў апрацоўкі вугал φ прымаецца роўным ад 10 да 90˚. Найбольш часта ўжываюцца разцы з кутом у плане φ = 45˚. Чым меншы галоўны кут у плане, тым чысцейшай атрымліваецца паверхня. Але з памяншэннем кута φ павялічваецца адціск разца ад нарыхтоўкі, змяншаецца дакладнасць апрацоўкі і могуць паўстаць вібрацыі, пры якіх працаваць практычна немагчыма.
Дапаможны кут у плане φ₁ - кут паміж праекцыяй дапаможнай рэжучай абзы на асноўную плоскасць і ўтваральнай апрацаванай паверхні. Дапаможны кут у плане ўплывае на чысціню апрацаванай паверхні і ў залежнасці ад умоў апрацоўкі выбіраецца ад 0 да 30˚.
Рэжучая прылада з кутом φ₁ = 0 дазваляе атрымаць малую шурпатасць пры вялікіх падачах (да 3 - 5 мм/аб).
Кутом пры вяршыні ε называецца вугал паміж праекцыямі галоўнай і дапаможнай рэжучых беражкоў на асноўную плоскасць. Чым больш гэты кут, тым лепш умовы адводу цяпла ад рэжучых беражкоў, тым больш устойлівасць разца.
Вугал паміж галоўнай рэжучай абзой і плоскасцю, праведзенай паралельна асноўнай плоскасці праз вяршыню разца, называецца вуглом нахілу галоўнай рэжучай абзы λ (мал. 4). Ён лічыцца станоўчым, калі вяршыня разца з'яўляецца найніжэйшай кропкай рэжучай абзы (мал. 4, а), і адмоўным, калі вяршыня разца з'яўляецца найвышэйшай кропкай абзы (мал. 4, б). Вугал λ роўны нулю, калі галоўны рэжучы кант паралельны асноўнай плоскасці (мал. 4, в).
Кут λ уплывае на масіўнасць галоўкі разца і кірунак сходу стружкі.
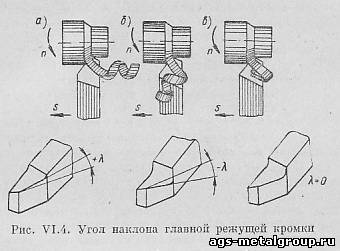
Пры нулявым або дадатным значэнні кута λ стружка сыходзіць у напрамку, зваротным падачы, пры гэтым яна будзе намотвацца на нарыхтоўку і драпаць апрацаваную паверхню. Але дадатнае значэнне кута λ робіць галоўку разца масіўней і больш устойлівай, а таму пры обдирочных працах, калі не прад'яўляецца высокіх патрабаванняў да якасці апрацаванай паверхні, рэкамендуецца дадатнае значэнне кута λ (да +5˚).
У разцоў з адмоўным значэннем кута λ кірунак сходу стружкі зваротнае, т. е. ад апрацаванай паверхні да апрацоўванай, але пры гэтым саслабляецца галоўка разца. Таму разцы з адмоўнымі кутамі λ прымяняюцца пры чыставой апрацоўцы.
§ 3. Элементы рэзання пры тачэнні
Да элементаў рэзання пры тачэнні адносяцца: скорасць рэзання, глыбіня рэзання і падача.
Хуткасцю рэзання υ называецца велічыня перамяшчэння паверхні рэзання адносна рэжучай абзы ў адзінку часу ў працэсе ажыццяўлення галоўнага руху.
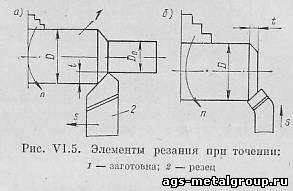
Пры такарнай апрацоўцы, калі апрацоўваная нарыхтоўка дыяметрам D (мал. 5, а) круціцца з некаторым лікам абарачэнняў n у хвіліну, хуткасць рэзання будзе змяняцца па даўжыні рэжучай абзы. Аднак у разліках хуткасці рэзання прымаецца яе максімальнае значэнне, якое вызначаецца па формуле дзе D - найбольшы дыяметр паверхні рэзання ў мм. Пры такарнай апрацоўцы адрозніваюць падоўжнае тачэнне, калі разец перамяшчаецца ў напрамку, паралельным восі нарыхтоўкі (мал, 5, а), і папярочнае тачэнне (мал. 5, б), калі разец перамяшчаецца ў напрамку, перпендыкулярным восі кручэння нарыхтоўкі.

У выпадку папярочнага тачэння, калі разец перамяшчаецца ад перыферыі да цэнтра ці, наадварот, ад цэнтра да перыферыі, хуткасць рэзання пры сталым ліку абарачэнняў зменная. Яна мае найбольшае значэнне ў перыферыі і роўна нулю ў цэнтры. Аднак і ў гэтым выпадку ў разлік прымаецца максімальная хуткасць рэзання, якая адпавядае дыяметру D.
Велічыня падачы s пры тачэнні вызначаецца перасоўваннем прылады за адзін абарачэнне нарыхтоўкі. У шэрагу выпадкаў бывае неабходна шляхта велічыню хвіліннай падачы sм.
Паміж падачай s (у мм/аб) і хвіліннай падачай sm (у мм/мін) існуе наступная залежнасць: sm = sn мм/мін, дзе n - лік абарачэнняў нарыхтоўкі ў хвіліну.
Глыбіня рэзання t - велічыня срезаемого пласта за адзін праход, вымераная ў кірунку, перпендыкулярным да апрацаванай паверхні (мал. 5, а). Глыбіня рэзання пры падоўжным тачэнні ўяўляе сабой паўрознасць паміж дыяметрам нарыхтоўкі і дыяметрам апрацаванай паверхні, атрыманай пасля аднаго праходу, Пры папярочным тачэнні за глыбіню рэзання прымаецца велічыня зразанага пласта (мал. 5, бы), вымераная ў восевым кірунку (перпендыкулярна да апрацаванай паверхні). З зменай падачы або глыбіні рэзання змяняецца папярочны перасек стружкі. На мал. 6 паказана папярочны перасек стружкі пры падоўжным тачэнні.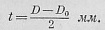
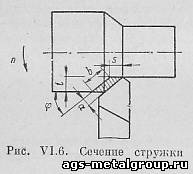
Шырынёй зрэзу b завецца адлегласць паміж апрацоўванай і апрацаванай паверхнямі, вымеранае па паверхні рэзання. Таўшчыня зрэзу α - адлегласць паміж двума паслядоўнымі становішчамі паверхні рэзання, атрыманае пасля аднаго абарачэння апрацоўванай дэталі.
Пры γ = 0, α = sin φ, b = t/sin φ, дзе φ - галоўны кут у плане.
Плошча папярочнага сячэння зрэзу f = αb = ts мм².
§ 4. Працэс утварэння стружкі
Заснавальнікамі навукі аб рэзанні металаў з'яўляюцца рускія вучоныя І; А. Ціме, К. А. Зварыкін і Я. Г. Усачоў. І. А. Ціме паказаў, што працэс адукацыі стружкі адбываецца па элементах (мал. 7, а).
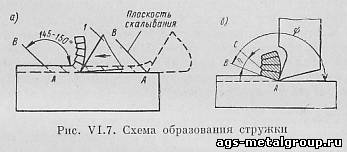
Разец 1 пры сваім руху дэфармуе які знаходзіцца перад ім метал; пры гэтым у зразаным пласце металу ствараецца пэўны напружаны стан. Калі напруга перавышае сілу ўнутранага счаплення часціц металу, адбываецца зрух элемента стружкі. Пры далейшым руху разца такой жа выявай адлучаюцца другі і наступныя элементы стружкі.
Плоскасць АВ, па якой адбываецца сколванне асобных элементаў стружкі, прынята зваць плоскасцю сколвання, а кут ψ паміж плоскасцю сколвання і кірункам руху разца - кутом сколвання. Кут сколвання для мяккіх металаў незалежна ад велічыні кута рэзання δ складае 145 - 150˚.
У працэсе рэзання перасоўванне (дэфармацыя) металу адбываецца ў зразаным пласце не толькі па плоскасці сколвання АВ, але і па так званай плоскасці зруху АС у межах кожнага элемента стружкі. Вугал паміж плоскасцю зруху АС і плоскасцю сколвання АВ называецца вуглом зруху η (мал. 7, б).
Асноўная дэфармацыя пры рэзанні пластычных металаў адбываецца па плоскасцях зруху, бо крышталі металу апыняюцца выцягнутымі ўздоўж гэтых плоскасцяў. Дзякуючы гэтаму трываласць металу ў стружцы менш па плоскасцях зруху, чым па плоскасцях сколвання. Гэта пацвярджаецца тым, што стружкі пры яе перагіне разломліваецца не па плоскасцях сколвання, а па плоскасці зруху.
У залежнасці ад умоў апрацоўкі стружкі можа быць розных відаў (мал. 8): зліўны, стружкі сколвання, надлому.
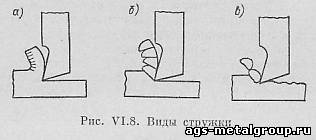
Глейкія металы (мяккая сталь, медзь, алюміній і т. д.) утвораць зліўныя стружкі, якія маюць выгляд суцэльнай прамой стужкі, плоскай або шрубавай спіралі. Асобныя элементы гэтай стружкі даволі трывала звязаны адзін з адным (мал. 8, а).
Пры апрацоўцы меней глейкіх металаў (сталяў падвышанай цвёрдасці, некаторых марак латуні і т. п.) утворыцца стружкі сколвання (мал. 8, бы). У яе выразна бачныя плоскасці сколвання паміж асобнымі элементамі, а верхні бок мае пилообразную форму. Элементы гэтай стружкі маюць менш трывалую сувязь, таму стружкі пасля адукацыі некалькіх завіткоў звычайна адломліваецца пад дзеяннем уласнай вагі.
Габлюшка надлому (мал. 8, у) атрымліваецца пры апрацоўцы далікатных металаў (чыгун, бронза) і неметалічных матэрыялаў. Сувязь паміж асобнымі элементамі стружкі настолькі слабая, што гэтыя элементы ўяўляюць сабой сукупнасць часціц няправільнай формы.
Выгляд якая ўтвараецца стружкі залежыць не толькі ад уласцівасцяў апрацоўванага металу, але таксама і ад хуткасці рэзання, геаметрыі разца і шэрагу іншых фактараў.
§ 5. Цеплавыя з'явы пры рэзанні металаў
У працэсе рэзання металаў выдзяляецца цяпло. Асноўнай крыніцай адукацыі цеплыні пры рэзанні з'яўляецца праца, затрачаная на дэфармацыю зразальнага пласта, трэнне стружкі аб перадпакой паверхня прылады і трэнне задняй паверхні разца аб паверхню рэзання. Даследаваннямі ўстаноўлена што больш за ўсё вылучаецца цеплыні ў выніку дэфармацыі зразальнага пласта.
Устаноўлена, што ў сярэднім пры такарнай апрацоўцы 50 - 86% усёй якая вылучаецца цеплыні сыходзіць у габлюшку, 40 - 10% - у разец, 9 - 3% - у апрацоўваную нарыхтоўку і каля 1% - у навакольнае асяроддзе. Пры павелічэнні хуткасці рэзання колькасць якая застаецца ў стружцы цеплыні значна павялічваецца, а паступленне яе ў разец і апрацоўваную дэталь адпаведна памяншаецца. Пры хуткасцях рэзання каля 100 м/мін [1,5 м/з] у стружцы застаецца каля 80% цеплыні, а пры хуткасцях парадку 500 м/мін [8 м/з] стружкай выносіцца 97 - 99% і толькі 1 - 3% цеплыні паступае ў разец, апрацоўваную дэталь і навакольнае паветра.
Больш за ўсё на тэмпературу ў зоне рэзання ўплывае хуткасць рэзання. Таму пры вялікіх хуткасцях рэзання, хоць дзель паступлення цеплыні ў прыладу і памяншаецца, агульная колькасць яе настолькі вяліка, што ў параўнанні са звычайнымі хуткасцямі рэзання ў значнай ступені павялічваюцца як тэмпература стружкі, так і тэмпература разца.
На тэмпературу рэзання ўплываюць падача, глыбіня рэзання, геаметрыя рэжучай часткі разца і яго памеры.
§ 6. Знос і стойкасць разцоў
Пад уплывам высокай тэмпературы, якая развіваецца ў працэсе рэзання і выклікае страту рэжучай часткай разца неабходнай цвёрдасці, а таксама з прычыны механічнага ізаляцыі граняў рэжучага кліну сыходнай стружкай і паверхняй рэзання разец зношваецца, затупляецца.
Пры тачэнні назіраецца знос рэжучай прылады як па яго перадпакоі, так і па задняй паверхням. На знос разца вялікі ўплыў аказваюць матэрыял апрацоўванай дэталі, рэжымы рэзання, геаметрыя прылады і якасць завострывання разца.
Найбольшая колькасць рэжучых інструментаў зношваецца ў асноўным па задніх паверхнях. У выніку зносу задняй паверхні каля рэжучай абзы утвараецца пляцоўка (мал. 9, а). Шырынёй h₃ гэтай пляцоўкі характарызуецца ступень зносу задняй паверхні.
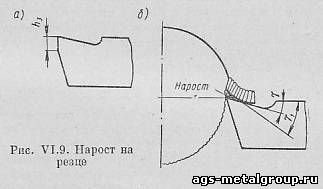
Выдатак рэжучай прылады і якасць апрацоўкі ў вялікай ступені залежаць ад затуплення прылады. Пры дасягненні вызначанай велічыні зносу павялічваюцца сілы рэзання, павялічваецца тэмпература рэзання, пагаршаецца чысціня апрацаванай паверхні, змяншаецца дакладнасць апрацоўкі.
Існуе некалькі крытэраў зносу разцоў. У вытворчых умовах за крытэр затуплення прымаецца адпаведная велічыня зносу.
Для такарных разцоў з пласцінкамі цвёрдых сплаваў рэкамендуюцца наступныя дапушчальныя значэнні h₃ (у мм)
Пры чарнавой апрацоўцы сталей........ 1,0 - 1,4 Пры чыставой апрацоўцы сталей ........ 0,4 - 0,6 » Чыгуна ...... 0,6 - 0,8
Для адразных разцоў з пласцінкамі цвёрдых сплаваў h₃ = 0,8 ÷ 1 мм. Для разцоў з керамічнымі пласцінкамі дапушчальная велічыня зносу h₃ = 0,6 ÷ 0,8 мм.
З паняццем аб зносе прылады непарыўна злучана паняцце пра яго ўстойлівасць. Устойлівасцю разца завецца той перыяд часу, на працягу якога яго знос пры бесперапыннай працы даходзіць да ўсталяванай велічыні, т. е. крытэра затуплення. Устойлівасць вымяраецца ў хвілінах і пазначаецца літарай Т. Яна залежыць ад такіх жа фактараў, як знос. Найбольшы ўплыў на знос і, такім чынам, на ўстойлівасць разца аказвае хуткасць рэзання. Звычайна рэжымы рэзання выбіраюцца такімі, каб устойлівасць разца Т была ў межах 30 - 60 мін.
З'явы цеплавыдзялення і зносу інструмента ўласцівыя любому віду апрацоўкі металаў (тачэнню, фрэзераванню, свідраванню і г. д.). Заканамернасці гэтых з'яў ляглі ў аснову пры прызначэнні рэжымаў рэзання.
|