ЭЛЕКТРЫЧНАЯ ДУГАВАЯ ЗВАРКА
§ 4. Віды электрадугавой зваркі
У прамысловасці найбольшае прымяненне маюць электрадугавая зварка прамога дзеяння з прымяненнем металічнага электрода 2 (мал. З, а) па спосабу Славянава і па спосабе Бенардоса (мал. З, б) з прымяненнем вугальнага неплавящегося электрода 3 і асадкавага прутка 4. Спосаб Бенардоса менш ужываецца, чым спосаб Славянава.
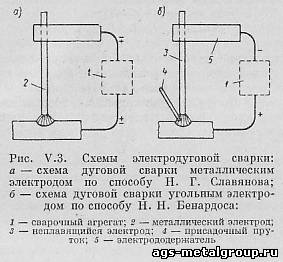
§ 5. Электрычная зварачная дуга і яе ўласцівасці
Электрычная зварачная дуга ўяўляе сабой магутны электрычны разрад у газавым асяроддзі. Газ пры нізкай тэмпературы не праводзіць электрычны ток. Газ можа праводзіць ток толькі пры наяўнасці ў ім па-электрычнаму зараджаных часціц-іёнаў, і ў гэтым выпадку яго завуць іянізаваным. Пры дугавым разрадзе вылучаецца значная колькасць цяпла, адбываецца іянізацыя газу.
Моцна іянізаваны газ слупа электрычнага разраду- дугі - валодае падвышанай электраправоднасцю, надыходзячай да электраправоднасці металаў, і забяспечвае падтрыманне ўстойлівага разраду пры мінанні току. Падставамі слупа дугавога разраду служаць рэзка абмежаваныя вобласці на паверхні электродаў - электродныя плямы (катодныя і анодныя).
Іянізацыя газу адбываецца ў асноўным у выніку саўдараў з малекуламі электронаў, якія імітуюць з паверхні адмоўнага электрода (катода). З павелічэннем сілы току павялічваецца кінэтычная энергія электронаў.
У дузе адбываецца ўзаемнае бамбаванне катода дадатнымі іёнамі і анода адмоўнымі іёнамі і электронамі; у выніку гэтага кінэтычная энергія часціц пераходзіць у цеплавую і адбываецца нагрэў і расплаўленне электрода і асноўнага металу.
Напружанне дугі паміж электродам і дэталлю галоўным чынам залежыць ад даўжыні дугі, сілы току, а таксама ад матэрыялу і памеру электродаў, цеплавога стану дугавога слупа, ступені яго іянізацыі і інш.
Для вызначэння напругі дугі спрошчана карыстаюцца наступнай эмпірычнай формулай: U = a + bL, дзе U - напруга дугі ва ў; L - даўжыня дугі ў мм; а і b- пастаянныя каэфіцыенты, якія вызначаюцца дасведчаным шляхам і якія залежаць ад матэрыялу электродаў, складу газавага асяроддзя і інш.; а - сума катоднага і аноднага падзення напругі дугі (роўная 10 - 12 у пры зварцы сталёвым электродам); b - сярэдняе падзенне напругі на адзінку даўжыні дугі, роўнае ў гэтым выпадку 2 - 3 у на 1 мм.
Для запальвання і падтрыманні дугі пры звычайнай зварцы ў выпадку выкарыстання сталёвых электродаў досыць напруга 45 - 50 у, а пры выкарыстанні вугальных электродаў - 55 - 65 у. Пасля ўсталявання дугавога разраду напруга падае і складае 18 - 25 у пры сталёвых электродах і 30 - 40 у - пры вугальных.
Крыніцай сілкавання электрадугі для зваркі можа быць сталы і зменны ток. Пры дугавой разрадцы тэмпература дугі дасягае ў цэнтры восевай яе часткі да 6000 - 7000' З у залежнасці ад сілы і шчыльнасці току.
Для атрымання высакаякаснага зварнога злучэння неабходна мець устойлівасць гарэння дугі і не дапушчаць яе перарывістасці.
Адлегласць паміж электродам і зварваным металам пры зварцы які плавіцца электродам павінна быць не больш за 0,6 - 0,8 дыяметра электрода; практычна даўжыня дугі ў гэтым выпадку складае 3 - 4 мм. Пры кароткай дузе адбываецца меншае насычэнне металу кіслародам і азотам, якія зніжаюць трываласць зварнога шва.
Устойлівасць дугі пры выкарыстанні сталага току значна вышэй, чым пры ўжыванні пераменнага току. Пры сілкаванні пераменным токам дуга меней устойлівая таму, што пры звычайнай частаце (50 гц) адбываецца сінусоідная змена напругі і току; ток у секунду 100 разоў мяняе свой кірунак, дуга перыядычна згасае і запальваецца і пры наяўнасці недастатковай іянізацыі паміж электродамі дуга можа перапыніцца.
Падвышэнне ўстойлівасці дугі дасягаецца ўжываннем пераменнага току падвышанай частаты - 150 - 450 гц, выкарыстаннем іянізавальных пакрыццяў электродаў (К₂СО₃, СаСО₃) або накладаннем токаў высокай частаты (т. у. ч.) на асноўны ток дугі, пры якім устойлівасць дугі атрымліваецца за рахунак іянізацыі дугавога слупа т. в. ч. У гэтым выпадку на электрод падаецца, акрамя напругі ад асноўнай крыніцы сілкавання, адначасова і напруга падвышанай частаты ад прыбора (асцылятара), якое дасягае да 10⁶гц, і напруга 2500 - 3000 у пры невялікай магутнасці 0,2 - 0,З квт.
Пры зварцы ўжываюць прамую і зваротную палярнасць. Пры прамой палярнасці мінус крыніцы току падлучаецца да электрода, а плюс - да якая зварваецца дэталі, а пры зваротнай палярнасці плюс падлучаецца да электрода, а мінус - да якая зварваецца дэталі.
Пры зварцы вугальным электродам на сталым току на прамой палярнасці дуга лягчэй узбуджаецца і ўстойлівей, чым пры зварцы на зваротнай палярнасці. Пры выкарыстанні металічных якія плавяцца электродаў палярнасць дугі менш уплывае на ўстойлівасць дугі, і зварка ажыццяўляецца як на пераменным, так і на сталым току з прамой і зваротнай палярнасцю ў залежнасці ад складу пакрыцця электродаў і флюсаў.
§ 6. Крыніцы харчавання зварачнай дугі
Для сілкавання зварачнай дугі ўжываюць адмысловыя крыніцы току. Калі пры звычайным сілкаванні токам асвятляльных лямпаў, электрарухавікоў і інш. варта мець сталую напругу ў сілкавальнай сетцы ў выглядзе амаль прамой лініі (мал. 4, а), раўналежнай восі абсцыс, то пры сілкаванні зварачнай дугі таго ці іншага тыпу неабходзен крыніца сілкавання току са спецыяльнай вальтампернай характарыстыкай (мал. 4, б).
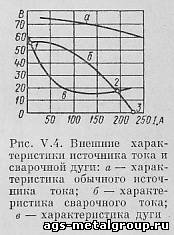
Доследная залежнасць напружання дугі ад току: пры пастаянных значэннях даўжыні дугі намалявана на мал. 4, у у выглядзе крывых.
У выпадку выкарыстання сілы току, звычайна ўжывальнага пры сучаснай дугавой ручной зварцы, напруга дугі амаль не залежыць ад сілы току. Напруга крыніцы току павінна памяншацца з павелічэннем зварачнага току і перасякаць у двух кропках 1 і 2 характарыстыку дугі. У кропцы 1 адбываецца ўзбуджэнне дугі, а ў кропцы 2 забяспечваецца ўстойлівае яе гарэнне. У момант кароткага замыкання ў кропцы 3 напруга крыніцы току памяншаецца да нуля. Напруга халастога ходу і крыніцы току павінна быць у 2,5 - 3 разу больш напругі дугі і складаць пры ручной дугавой зварцы металічным электродам сталым токам 45 - 65 у, а зменным токам - 55 - 100 а.
Сілкаванне зварачнай дугі пры зварцы на сталым току ажыццяўляецца ад адмысловага зварачнага генератара. Зварачныя генератары падпадзяляюцца на однопостовые для сілкавання аднаго зварачнага паста і многопостовые прызначаныя для сілкавання адначасова некалькіх зварачных пастоў. Акрамя таго, генератары бываюць стацыянарныя і перасоўныя, якія працуюць ад электрарухавіка ці ад рухавіка ўнутранага згарання.
У прамысловасці значная колькасць зварачных пастоў працуе ад пераменнага току. Сілкаванне зварачных пастоў пераменным токам вырабляецца ад зварачных трансфарматараў, якія паніжаюць напругу, якое існуе ў завадской сетцы (220, 380 у да 60 - 65 у).
Пры зварцы пераменным токам падальную знешнюю характарыстыку атрымліваюць уключэннем паслядоўна з дугой у зварачны ланцуг дастатковага індуктыўнага супраціву. Гэта дасягаецца ўключэннем у другасны ланцуг трансфарматара паслядоўна з дугой індуктыўнага супраціву дросельнай шпулькі, аддзеленай ад трансфарматара (мал. 5, а) або аб'яднанай з ім у адно цэлае (мал. 5, бы). Маюцца зварачныя трансфарматары (тып СТН) з павялічанай індуктыўнасцю без дросельнай шпулькі.
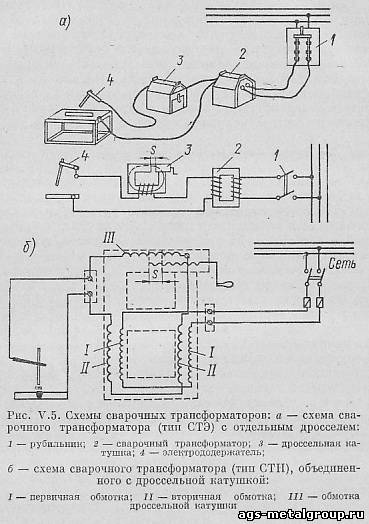
Першасная абмотка трансфарматара (мал. 5, а) падлучаецца да сілавой сеткі, а другасная - да зварачнага посту. Сардэчнік дросельнай шпулькі складаецца з двух частак - нерухомай, на якой маюцца віткі шпулькі, і рухомай, якая перамяшчаецца паваротам ручкі. Электрычны супраціў дросельнай шпулькі памяншаецца пры павелічэнні зазору S паміж рухомай і нерухомай часткамі стрыжняў, у сувязі з чым павялічваецца сіла току ў зварачным ланцугу; пры памяншэнні зазору паміж часткамі стрыжня ўзрастае электрычны супраціў дросельнай шпулькі і памяншаецца велічыня зварачнага току.
Зварачныя трансфарматары з аб'яднанай з імі дросельнай шпулькай СТН, распрацаваныя акад. В. П. Нікіціным, прызначаюцца для харчавання дугі пры зварцы на токах 500, 1000, 2000 а. На мал. 5, бы прыведзена схема зварачнага трансфарматара СТН-500 (СТН-700). Сілкаванне зварачнай дугі можа ажыццяўляцца выпрамніком, уяўлялым спалучэнне зварачнага трансфарматара з выпроствальнай прыладай, у якім выкарыстоўваюцца выпроствальныя элементы - селенавыя, германіевыя ці крамянёвыя. К. п. д. такіх зварачных агрэгатаў значна перавышае к. п. д. маторагенератарных установак.
§ 7. Электроды і флюсы
Пры электродуговой зварцы ўжываюць электроды металічныя якія плавяцца (сталёвыя, чыгунныя, з каляровых металаў) і неплавальныя вугальныя, графітавыя і вальфрамавыя (пры зварцы ў інэртных газах). Металічныя плавячыя электроды ўжываюць пры зварцы па спосабе Славянава; вугальныя, графітавыя- па спосабе Бенардоса, вальфрамавыя - пры атамнавадароднай і аргонодуговой зварцы.
Вугальныя электроды вырабляюць Ø 6 - 30 мм і даўжынёй да 300 мм. Сталёвыя электроды для ручной зваркі вырабляюць з адмысловага зварачнага дроту Ø 1 - 12 мм па ДАСЦЕ 2246 - 70 і шэрагу адмысловых ТУЮ. Зварачны дрот прымяняецца вугляродзісты, легіраваны і высокалегіраваны. Утрыманне вугляроду ў дроце, як правіла, абмяжоўваецца, што паляпшае пластычнасць наплаўленага металу. Вугляродзісты зварачны дрот маркі Св. 08 змяшчае вугляроду не звыш 0,10%; ужываецца для выраба шэрагу марак электродаў і для аўтаматычнай зваркі.
Для падвышэння трываласці наплаўленага металу ўжываюць зварачны дрот з падвышаным утрыманнем марганцу- Св. 08Г (0,80 - 1,10% Мn) і Св. 10Г2 (1,50 - 1,90% Мn). Марганец раскісляе метал, перашкаджае адукацыі гарачых расколін.
Легіраваны і высоколегированный зварачны дрот ужываюць для зваркі адпаведна легіраваных і высоколегированных вырабаў. Пры аўтаматычнай зварцы зварачны дрот выкарыстоўваецца ў выглядзе маткоў.
Для ручной дугавой зваркі дрот наразаюць даўжынёй 250-450 мм. Электроды Ø 1 - 2 мм ужываюць для зваркі металу таўшчынёй да 2 мм, а электроды Ø З мм - для зваркі металаў таўшчынёй 2 - 4 мм. Для зваркі металаў таўшчынёй 5 - 10 мм выкарыстоўваюцца электроды Ø 4 - 5 мм, а пры зварцы 6вялікай таўшчыні - электроды Ø 5 - 8 мм.
Сталёвыя электроды для ручной электрадугавой зваркі пакрываюць адмысловымі абмазкамі для абароны расплаўленага металу ад насычэння яго кіслародам і азотам, для стварэння ўстойлівасці гарэння дугі і надання наплаўленаму металу адмысловых уласцівасцяў, якія залежаць ад наяўнасці легавалых элементаў у складзе абмазкі. Электродныя абмазкі прымяняюцца двух відаў - тонкія і тоўстыя. Тонкія абмазкі электродаў (звычайна крэйда і вадкае шкло) прызначаюцца толькі для павелічэння ўстойлівасці гарэння дугі і іх ужываюць для зваркі малаадказных вырабаў з вугляродзістай сталі.
Для зваркі адказных вырабаў ужываюць электроды з тоўстай абмазкай (пакрыццём). Таўшчыня пласта пакрыцця звычайна складае каля 1 мм пры адноснай вазе пакрыцця каля 15 - 35% ад вагі электроднага стрыжня. У склад пакрыцця электродаў уваходзяць шлакаўтваральныя, газаўтваральныя, якія легуюць і клеючыя ці злучныя рэчывы і раскісляльнікі.
Шлакаўтваральныя і клеючыя рэчывы, а таксама раскісляльнікі маюцца, як правіла, ва ўсіх якасных тоўстых пакрыццях. Астатнія складнікі ўводзяцца на ўсе пакрыцці. Шлакаўтваральныя рэчывы прызначаюцца для падвышэння ўстойлівасці дугі і для абароны расплаўленага металу шлакавай абалонкай ад уздзеяння кіслароду і азоту. Яны складаюцца ў асноўным з вокіслаў металаў і металоідаў у выглядзе тытанавага канцэнтрату (ільменіту), марганцевой руды (піралюзіту), палявога шпата, мармуру, мелу і інш.
Газаўтваральныя складнікі выкарыстоўваюцца ў пакрыццях для стварэння падчас плаўлення электрода газавага ахоўнага асяроддзя вакол слупа дугі і расплаўленага металу. Ахоўнае асяроддзе складаецца або з вокісу вугляроду, або з некаторых прадуктаў распаду вугляводаў. Гэтыя газы засцерагаюць расплаўлены метал ад уздзеяння кіслароду і азоту паветра, але самі з'яўляюцца акісляльнікамі, у сувязі з чым у пакрыцці ўводзяць дастатковую колькасць раскісляльнікаў.
Якія легуюць складнікі і раскісляльнікі -(ферромарганец, ферасіліцый, фераванадый, ферахром, фератытан, алюміній і інш.) уводзяць у абмазку ў выглядзе тонказдробненага парашка разам са шлакообразующими і газаўтваральнымі матэрыяламі. Іх прызначэнне - павышэнне механічных уласцівасцей наплаўленага металу і наданне яму спецыяльных уласцівасцей (жараўстойлівасці, зносаўстойлівасці і інш.).
Пры зварцы частка, якія легуюць элементаў стрыжня і электроднага пакрыцця выгарае, а іншая частка пераходзіць у наплаўлены метал.
Для зваркі высоколегированных сталей ужываюць электроды з высоколегированного дроту, якая мае прыкладна такі ж хімічны склад, як і метал, які зварваецца. У склад абмазкі такіх электродаў, акрамя шлакаўтваральных і газаўтваральных матэрыялаў, уводзяць легіруючыя элементы для кампенсацыі іх чаду.
У якасці раскісляльнікаў пры зварцы сталей прымяняюцца марганец, тытан, крэмній і алюміній, якія маюць большае падабенства з кіслародам, чым жалеза, дзякуючы чаму адбываецца аднаўленне жалеза з яго вокіслаў.
У залежнасці ад патрабаванняў, якія прад'яўляюцца да, якасці зварнога шва, ужываюць электроды: Э34, Э42 і інш. для зваркі вугляродзістых і нізкалегіраваных сталей; ЭМ, ЭХМ і інш. для зваркі цеплаўстойлівых среднелегированных сталей ЭА-ЗМ6, ЭА2Б (аўстэнітнага тыпу), ЭФ-13 і інш. (ферытнага тыпу); ЭНГ-62, ЭНГ-50 і інш. для наплавак з мэтай атрымання высокай цвёрдасці.
Вялікае значэнне мае марка, які ўжываецца тыпу электрода, якая характарызуе склад пакрыцця электрода, яго тэхналагічныя ўласцівасці: род і палярнасць току для зваркі і наплаўкі і інш.
Распаўсюджаныя высакаякасныя электроды марак ОММ-5 і УОНИ 13/55, якія адпавядаюць маркам Э42 і Э55 (ДАСТ 9467 - 60), маюць наступныя склады абмазак: электрод ОММ-5 - 37% тытанавага (ільменітавага) канцэнтрату, 21 % марганцу , 13% палявога шпата, 20% ферромарганцу, 9% крухмалу і 30% (ад вагі кампанента) вадкага шкла; электрод, маркі УОНИ 13/55 - 54% мармуру СаСО₃, 15% плавікавага шпата, 9% кварца SiO₂, 5% феромарганцу, 5% ферасіліцыя, 12% фератытану і 30% (ад вагі кампанента) вадкага шкла. Назоўнік паказвае ніжнюю мяжу трываласці пры расцяжэнні наплаўленага металу ў кг/мм².
Большасць электродаў вырабляюць на адмысловых заводах або ў электродных майстэрнях, дзе вытворчыя аперацыі (рубка дроту, раздрабненне памол і перамешванне матэрыялаў са злучнымі; пакрыццё электродаў абмазкай), цалкам механізаваны.
Нанясенне пакрыццяў вырабляецца або акунаннем электродаў у ванну з вадкай обмазочной масай з наступным павольным уздымам электрода з ванны, або больш дасканалым метадам; нанясеннем пакрыцця на электрод, апрасоўкай адмысловымі электроднымі прэсамі, якія працуюць пад ціскам 40 - 50 М (40 - 50 М) У гэтым выпадку электродны стрыжань, прапускаецца праз муштук прэса і разам з ім выціскаецца электродная маса, раўнамерна якая пакрывае са ўсіх бакоў стрыжань. Пры выхадзе з прэса адзін канец электрода чысцяць ад абмазкі для
захопу яго электрадатрымальнікам. Прадукцыйнасць такіх прэсаў – 100 – 400 электродаў у хвіліну.
Пакрытыя электроды падвяргаюцца сушцы пры ўмераных тэмпературах, якія залежаць ад складу.
|