§ 29. Сутнасць працэсу і вобласць прымянення
Ліставай штампоўкай называюць метад вырабу плоскіх і аб'ёмных танкасценных вырабаў з ліставага матэрыялу, стужкі або паласы з дапамогай штампаў на прэсах або без прымянення прэсаў (беспрэсавая штампоўка). Ліставая штампоўка дзеліцца на гарачую і халодную.
Гарачая ліставая штампоўказ'яўляецца меней распаўсюджаным працэсам, яна ўжываецца ў вытворчасці кацельняў дна, паўшар'яў, буяў і іншых карпусных дэталяў для суднабудавання, якія вырабляюцца з сталёвага ліста таўшчынёй звыш 3 - 4 мм. Асноўнымі аперацыямі гарачай ліставай штампоўкі з'яўляюцца выцяжка полых сферычных вырабаў з плоскай нарыхтоўкі, выразанай папярэдне на дыскавых нажніцах, высечка дэталяў, а таксама гнуткая клямараў і іншых вырабаў з полосовой сталі і тоўстага ліста. Ужывальнае абсталяванне: гідраўлічныя, кривошипные і фрыкцыйныя прэсы.
Халодная ліставая штампоўка- найболей прагрэсіўны метад апрацоўкі ціскам, атрымалы шырокае ўжыванне ў прамысловасці. Халоднай штампоўкай вырабляюць як вельмі буйныя дэталі - рамы і кузавы аўтамабіляў, дэталі фюзеляжаў і шасі самалётаў, элементы ашалёўкі судоў, так і вельмі дробныя - дэталі гадзіннікавых механізмаў, радыёлямп, аўтаручак.
Да тэхніка-эканамічных пераваг халоднай штампоўкі перад іншымі відамі апрацоўкі металаў адносяцца: эканомнае выкарыстанне матэрыялу (адходы не больш за 15 - 20%); масавы выпуск і нізкі кошт вырабаў з высокай дакладнасцю памераў і добрай якасцю паверхні; найвышэйшая прадукцыйнасць абсталявання з поўнай механізацыяй і аўтаматызацыяй вытворчасці (выпуск невялікіх дэталяў дасягае 50 - 60 тыс. шт. у змену з аднаго прэса-аўтамата); магчымасць атрымання полых танкасценных вырабаў вельмі складаных формаў, якія не маюць патрэбы ў наступнай апрацоўцы іх на станках і з'яўляюцца гатовымі ўзаемазаменнымі дэталямі, а не нарыхтоўкамі; прастата працы на штамповачных прэсах і магчымасць абслугоўвання іх малакваліфікаванымі працоўнымі.
Халодная штампоўка, якая дае найбольшы эфект у масавай і буйнасерыйнай вытворчасці, паспяхова ўжываецца і ва ўмовах дробнасерыйнай вытворчасці, пры выпуску дэталяў 5 - 10 тыс. шт. у год. Зыходным матэрыялам для халоднай ліставай штампоўкі з'яўляюцца лісты і стужкі з розных металаў і сплаваў і неметалічных матэрыялаў: выкарыстоўваюцца лушчак, скура, фібра, тэксталіт, цэлулоід, гетынакс і іншыя пластмасы. Таўшчыня ліставых матэрыялаў звычайна не перавышае 3 - 5 мм.
§ 30. Тэхналогія ліставай штампоўкі
Аперацыі ліставай штампоўкі дзеляцца на два асноўных класа: раздзяляльныя , у якіх адна частка нарыхтоўкі аддзяляецца ад іншай, і формазмяняльныя, Пры якіх атрымліваюць вырабы складанай формы за кошт перамяшчэння элементарных аб'ёмаў матэрыялу зыходнай нарыхтоўкі без яе разбурэння. Ужываюць таксама зборачныя аперацыі, пры якіх асобныя дэталі пад ціскам штампа злучаюцца ў агульны вузел.
Да асноўных раздзяляльных аперацый адносяцца адрэзка, высечка і прабіўка.
Да асноўных формоизменяющих аперацыях ставяцца гнуткая, выцяжка, абціск, отбортовка, фармоўка.
Рэзка- паслядоўнае аддзяленне часткі нарыхтоўкі па прамой ці крывой лініі. Рэзка ўжываецца звычайна як нарыхтоўчая аперацыя для раскрою ліста на палосы зададзенай шырыні, якія паступаюць затым на штампоўку высечкай. Рэзка выконваецца звычайна на гільяцінных нажніцах з верхнім нахіленым нажом, якія разразаюць ліст па прамой лініі; рэзанне нарыхтовак з крывалінейным контурам выконваюць на дыскавых або вібрацыйных нажніцах (пры малой таўшчыні ліста). Рэзанне невялікіх нарыхтовак (палосак) выконваецца штампамі, усталяванымі на кривошипных прэсах.
Для атрымання дакладнай зададзенай шырыні паласы або даўжыні нарыхтоўкі нажніцы і штампы забяспечваюцца ўпорамі.
Высечка - аперацыя аднаразовага аддзялення матэрыялу ад нарыхтоўкі па замкнёным контуры, прычым якая адлучаецца частка з'яўляецца вырабам.
Прабіўка- атрыманне адтулін шляхам аддзялення матэрыялу па замкнёным контуры ўнутры дэталі. Пры прабіўцы якая адлучаецца частка з'яўляецца адыходам. Адрозненне гэтых аперацый складаецца толькі ў іх прызначэнні, бо працэс дэфармавання металу і прылада ўжывальных для гэтых аперацый штампаў па істоце аднолькавыя. Высечку і прабіўку (мал. IV.40, а, б) выконваюць пуансонам, які ўціскае якая адлучаецца частку нарыхтоўкі ў адтуліну матрыцы. Працоўныя беражкі пуансона і матрыцы павінны быць вострымі, а зазор паміж пуансонам і адтулінай матрыцы (на бок) павінен складаць 5 - 10% таўшчыні нарыхтоўкі. Пры прабіўцы, калі задаюцца памеры адтуліны, памеры перасеку пуансона бяруць роўнымі памерам адтуліны і памеры адтуліны матрыцы павялічваюць на велічыню зазору; пры высечцы памеры адтуліны матрыцы выконваюць па памерах выраба, а памеры пуансона - на зазор менш.
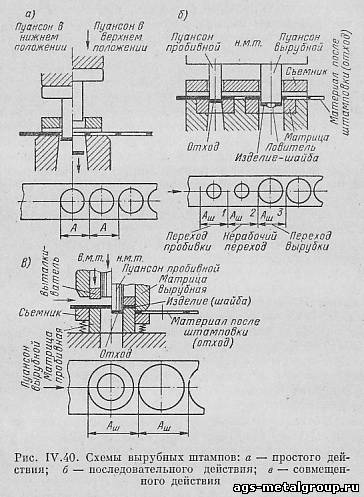
Для павышэння дакладнасці памераў штампуемых дэталяў да 3- 2а класаў і чысціні паверхні да 7 - 8-га класаў у вытворчасці гадзін і дакладных прыбораў прымяняецца зачыстка - аперацыя зразання няроўнасцяў, якія засталіся пасля высечкі або прабіўкі.
Высілак, неабходнае для выканання высечкі і іншых падзяляльных аперацый, вызначаюць, множачы пляц перасеку адначасова разразанага матэрыялу на ўдзельнае супраціў яго зрэзу.
Гнуткая- формазмяняльная аперацыя для атрымання выгнутай дэталі з плоскай нарыхтоўкі. Гнуткая бывае аднавуглавая V-вобразная (мал. IV.41, а), двухвуглавая U-вобразная (мал. IV. 41, б) і шматкутная. Пры гнутцы адбываецца сціск унутраных пластоў металу, прылеглых да пуансона, і расцяжэнне вонкавых пластоў, прылеглых да матрыцы, у кірунку даўжыні нарыхтоўкі. Гэтыя дэфармацыі будуць тым большыя, чым меншы радыус выгібу r. Пласт металу, які не адчувае ні сціску, ні расцяжэння, называецца нейтральным. Гэты пласт размешчаны прыкладна пасярэдзіне таўшчыні матэрыялу, і па яго разгорнутай даўжыні, падлічанай па чарцяжы дэталі, вызначаецца даўжыня нарыхтоўкі.
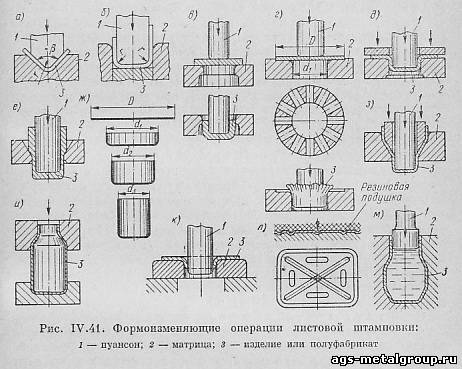
Метал варта гнуць перпендыкулярна да напрамку пракаткі, каб сціск і расцяжэнне ад выгібу ішло ў напрамку валокнаў металу. Пры гэтым дасягаюцца мінімальныя радыусы гнуткія.
Выцяжка- аперацыя, якая ператварае плоскую нарыхтоўку ў полую дэталь або паўфабрыкат. Пры выцяжцы (мал. IV.41, а) плоская нарыхтоўка (напрыклад, высечаная кружэлка) пад ціскам пуансона паступова ўцягваецца ў адтуліну матрыцы. Сярэдняя частка, якая ўтварае дно будучага каўпачка, апускаючыся ў адтуліну матрыцы, цягне за сабой астатнюю колцавую частку нарыхтоўкі- фланец шырынёй D - d₁ (мал. IV. 41, г). Пры гэтым лішнія аб'ёмы металу фланца ў выглядзе трохкутных сектараў з таўшчынёй, роўнай таўшчыні нарыхтоўкі, падвяргаюцца дзеянню тангенцыйных сціскальных высілкаў і пасля ўцягвання ў зазор ідуць на павелічэнне вышыні шкляначкі. Калі таўшчыня матэрыялу значная ў параўнанні з дыяметрам дэталі (мал. IV.41, у), а форма матрыцы не перашкаджае плыўнаму ўцягванню ў яе нарыхтоўкі, той уплыў сціскальных высілкаў выявіцца ў некаторым патаўшчэнні матэрыялу ў верхняга (тарцавога) боку дэталі. Пры адсутнасці гэтых умоў сціскальныя напругі выклікаюць адукацыю зморшчын (гофраў), якія з'яўляюцца на краях нарыхтоўкі амаль адразу пасля пачатку выцяжкі і распаўсюджваюцца затым на ўсю вышыню сценак (мал. 41, г), выклікаючы шлюб выраба. Для прадухілення гэтага частка нарыхтоўкі, якая ляжыць на матрыцы, утрымліваюць спецыяльным прыціскным кольцам (мал. 41, д).
Выцяжкай можна вырабляць не толькі цыліндрычныя дэталі, але і больш складаныя па форме: коробчатые, канічныя, паўсферычныя. Падвяргаюцца выцяжцы і паўфабрыкаты, атрыманыя папярэдняй выцяжкай (мал. 41, з). Выцяжка за адзін пераход рэгламентуецца трываласцю выцягваецца шкляначкі. Спроба ўцягнуць у матрыцу занадта вялікую па памерах нарыхтоўку прыводзіць да адрыву дна. Магчымасць выцяжкі вызначаецца каэфіцыентам выцяжкі m₁ уяўляе сабой стаўленне дыяметра выцягванага каўпачка d₁ да дыяметра нарыхтоўкі D (мал. 41, г). Гэты каэфіцыент павінен быць не менш за 0,5 – 0,6. Калі ён па разліку атрымліваецца менш, то дэталь выцягваюць за два і больш пераходу (мал. 41, ж), пры гэтым каэфіцыент выцяжкі m₂ = d₂/d₁, m₃ = d₃/d₄ і г. д. прымаюць не менш за 0,7 - 0,8. Ведаючы каэфіцыенты выцяжкі, можна вызначыць і аперацыйныя памеры паўфабрыкатаў: d₁ = Dm₁; d₂ = d₁m₂ і г. д. Пры неабходнасці атрымаць полае выраб з тонкімі сценкамі (да 0,1 мм і менш) і вялікай вышыні ўжываюць выцяжку з утонением матэрыялу (мал. 41, е), пры гэтым велічыня зазору бярэцца менш зыходнай таўшчыні матэрыялу . Таўшчыня дна дэталі пры гэтым застаецца нязменнай. Высілак выцяжкі набліжана можна вызначыць, памнажаючы пляц папярочнага перасеку выцягванага каўпачка на мяжу трываласці металу.
Абціск - аперацыя звужэння канцавой часткі полых або аб'ёмных дэталяў шляхам абціску матэрыялу штампам звонку ў канічнай матрыцы (мал. 41, і).
Отбортовка і разбортовка - адукацыя бартоў па вонкавым контуры нарыхтоўкі ці вакол прабітых адтулін за рахунак расцяжэння матэрыялу (мал. 41, да). Гэтыя аперацыі выконваюцца за адзін ці некалькі пераходаў у штампах на прэсах або паступовым дэфармаваннем металу ролікамі (буйныя дэталі).
Фармоўка- аперацыя, якая змяняе форму нарыхтоўкі або паўфабрыката з дапамогай мясцовых дэфармацый, напрыклад выраб рэбраў калянасці (зіг), павелічэнне дыяметральных памераў сярэдняй часткі полай дэталі (мал. 41, л, м). Раздача сярэдняй часткі выцягнутай шклянкі ажыццяўляецца з дапамогай гумовага ўкладыша, сталёвых шарыкаў ці вадкасці ў раздымнай матрыцы.
Распрацоўка тэхналагічнага працэсу ліставай штампоўкі вядзецца ў наступным парадку:
1) усталёўваецца структура працэсу, т. е. характар, колькасць і паслядоўнасць аперацый;
2) выконваюцца неабходныя разлікі па ўстанаўленні памераў нарыхтоўкі, аперацыйных памераў паўфабрыкатаў, намаганняў штампоўкі і т. п.;
3) працэс афармляецца ў адпаведнай тэхналагічнай дакументацыі.
Па структуры тэхналагічны працэс складаецца з асноўных аперацый, да якіх адносяцца: рэзка ліста на палосы, высечка, выцяжка, гнуткая і іншыя штамповачныя, а часам і зборачныя аперацыі, і дапаможных аперацый: ачысткі, праўкі і змазкі лістоў, адпалу і тручэння гатовых вырабаў, іх галтоўкі, нанясенні ахоўных ці дэкаратыўных пакрыццяў (храміравання, нікеліраванні і т. п.).
Разлік памераў нарыхтоўкі неабходзен для тых дэталяў, атрыманне якіх злучана з аперацыямі прасторавай змены формы, т. е. выгнутых, полых і аб'ёмных. Разлік памераў і формы нарыхтовак гнутых дэталяў вырабляюць шляхам разгортвання (умоўнай разгінанні) дэталі ў плоскую. Пры гэтым лічаць, што даўжыня прамых участкаў дэталі застаецца пасля гнуткі нязменнай, а даўжыня выгнутых участкаў роўная даўжыні нейтральнага пласта. Палажэнне нейтральнага пласта можна знайсці па набліжанай формуле: ρ = √r(r + t), дзе ρ - радыус нейтральнага пласта; r - радыус гнуткавага пуансона (r ≥ 0,5t); t - таўшчыня матэрыялу.
Памеры нарыхтоўкі для дэталей, якія вырабляюцца выцяжкай, вызначаюць па роўнасці пляцаў паверхні нарыхтоўкі Fз і гатовай дэталі Fд (з прыпускам на абразанне). Паверхня гатовых дэталяў, уяўлялых сабой цела кручэння складанай формы, вызначаюць шляхам падсумоўвання пляцаў f асобных простых геаметрычных элементаў, яе ўтваральных (круг, цыліндр, кольца і т. п.). Дыяметр загатоўкі D знаходзяць з формулы: D = 1,13√Fд = 1,13√Σf.
Аперацыйныя памеры, т. е. памеры, якія атрымлівае нарыхтоўка (або паўфабрыкат) пасля выканання дадзенай аперацыі, разлічваюць для выгнутых і полых дэталяў у зваротным парадку- ад апошніх аперацый да першых. Пасля іх вызначэння і выбару памераў нарыхтоўкі усталёўваюць расчыні матэрыялу. Пад раскроем разумеюць найвыгаднае размяшчэнне высякае дэталяў на палосах або стужках матэрыялу, якія паступаюць у вырубной штамп. Раскрой паласы павінен забяспечыць найлепшую якасць дэталі, эканомнае выкарыстанне матэрыялу, прастату канструкцыі штампа, зручнасць і бяспеку яго працы. Для атрымання чысціні зрэзу высечанай нарыхтоўкі, а таксама для памяншэння задзірын і коробления рэкамендуецца весці высечку з перамычкамі, шырыню якіх бяруць мінімальнай, роўнай адной-двум таўшчыням зыходнага металу.
На аснове абраных выгляду раскрою і штамповачных аперацый выбіраюць неабходнае абсталяванне і ў дачыненні да яго распрацоўваюць канструкцыі штампаў.
|