Прэсаванне і валачэнне металаў
§ 11. Сутнасць працэсу прасавання
Прэсаванне доўгіх вырабаў складанага профілю ажыццяўляецца на магутных гідраўлічных прэсах. Нагрэты злітак 3 (мал. IV.16, а) цыліндрычнай формы змяшчаецца ў паражніну таўстасценнага сталёвага цыліндру 4, званага кантэйнерам прэса; з іншага боку кантэйнера замацоўваецца матрыца 2 з гарачатрывалай сталі (ЗХВ8 або 5ХВС), мелая адтуліна, якое адпавядае па форме перасеку прасаванага выраба.
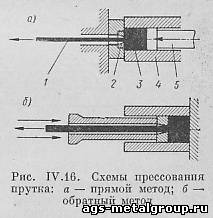
Ціск на метал перадаецца пуансонам бы (шплінтанам), на канцы якога ўмацаваная зменная прессшайба, шчыльна якая ўваходзіць у паражніну кантэйнера. Пуансон цвёрда злучаны з галоўным поршнем (плунжарам) гідраўлічнага цыліндру прэса, у які паступае вада пад ціскам 150 - 200 ат (14,7 - 19,6 Мпа). Дыяметр галоўнага плунжера прэса дасягае 2000 мм і больш, таму ўдзельны ціск прессшайбы, мелай параўнальна невялікі дыяметр (60 - 500 мм), на метал вельмі вяліка і дасягае 10000 кг/см² (981 Мпа). Прессшайба, павольна перасоўваючыся ўздоўж кантэйнера, выціскае металічны пруток 1 праз адтуліну матрыцы. У канцы аперацыі ў кантэйнеры застаецца невялікая частка злітка, званая прессостатком, якая змяшчае звычайна недабраякасны метал. Зваротны ход пуансона з прессшайбой ажыццяўляецца двума зваротнымі цыліндрамі,
Адметнай асаблівасцю прасавання з'яўляецца наяўнасць рэзка выяўленай схемы ўсебаковага нераўнамернага сціску металу (пад дзеяннем прессшайбы і за рахунак супрацьціску сценак кантэйнера), што значна павялічвае яго пластычнасць. Таму прасаваннем апрацоўваюцца і малапластычныя металы, і сплавы, апрацоўка якіх ціскам іншымі спосабамі прыводзіць да шлюбу (у выніку адукацыі расколін).
Зыходным матэрыялам для прасавання служаць зліткі з каляровых металаў: медзі, алюмінія і іх сплаваў (бронзы, латуні), нікелевых і магніевых сплаваў, а таксама зліткі са сталі. Дыяметр зліткаў з каляровых сплаваў складае 50 - 800 мм пры даўжыні 120 - 1800 мм.
Прэсаваннем атрымліваюць складаныя профілі рознага перасеку даўжынёй да 25 - 35 м (мал. IV.17, а) і пруткі дыяметрам 5 - 200 мм, трубы гладкія і рабрыстыя дыяметрам да 400 мм і вышэй пры таўшчыні сценак 1,5 - 8 мм. Пруткі невялікага дыяметра атрымліваюць прасаваннем праз некалькі адтулін у адной матрыцы.
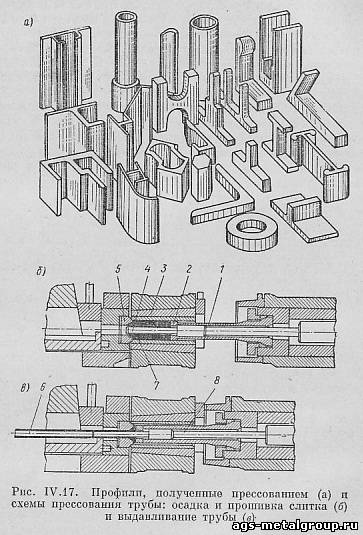
Прынцып прасавання выкарыстоўваецца і пры гарачай штампоўцы ў зачыненых штампах вырабаў з легаванай сталі: клапанаў аўтатрактарных рухавікоў, турбінных лапатак і інш., а таксама пры лядоўні штампоўцы выдушваннем пустотелых танкасценных вырабаў з таўсталіставай нарыхтоўкі.
Механічныя ўласцівасці вырабаў залежаць ад ступені абціску зыходнага адліванага металу. Чым яна больш, тым драбней будзе крышталічная структура гатовага прадукта і тым вышэй атрымліваюцца яго механічныя ўласцівасці.
Пры прэсаванні адрозніваюць дзве хуткасці, якія характарызуюць працэс: хуткасць прасавання υn, з якой рухаецца прессшайба ў кантэйнеры, і хуткасць заканчэння υu, якая ўяўляе сабой хуткасць выцякання металу праз ачко матрыцы. Гэтыя хуткасці злучаны суадносінамі: υu = λυn, дзе λ - каэфіцыент выцяжкі, роўны стаўленню пляцаў папярочных перасекаў паражніны кантэйнера і адтулін матрыцы. Пры прэсаванні λ = 8 ÷ 50. Пры вельмі вялікіх скорасцях заканчэння ў пруткі ўтвараюцца расколіны, «яршы» і іншыя дэфекты. Хуткасць заканчэння для дуралюміна роўная 3 - 6 гл/сек, магніевых сплаваў 4 - 50 гл/сек, алюмінія 10 - 250 гл/сек, медзі і яе сплаваў 10 - 500 гл/сек.
§ 12. Тэхналогія прасавання
Адрозніваюць два асноўныя метады прасавання: прамы (гл. мал. IV.16, а) і адваротны (мал. IV.16, б).
Прамы метадпрасавання апісаны ў § 11 і ўжываецца для пруткоў, складаных профіляў і труб. Прэсаванне па зваротным метадзепрымяняецца галоўным чынам для атрымання пруткоў. У гэтым выпадку шплінтан робіцца полым, і на яго канцы ўмацоўваецца матрыца. Падчас руху шплінтана злева направа матрыца, гуляючая адначасова і роля прэсшайбы, душыць на кантавую частку злітка, пры гэтым метал змушаны выцякаць у зваротным кірунку, бо паражніна кантэйнера з процілеглага канца зачынена масіўнай упартай шайбай. Калі пры прамым прэсаванні ўся маса злітка перамяшчаецца ў кантэйнеры ў кірунку плыні металу, то пры зваротным прэсаванні злітак нерухомы адносна сценак кантэйнера, з прычыны чаго значна памяншаецца дзеянне сіл трэння пры прэсаванні. У выніку высілак прасавання зваротным метадам змяншаецца на 25 - 30%.
Да пераваг зваротнага метаду ставіцца таксама і зніжэнне страт металу ў прэсастатак, які з 15 - 18% ад вагі злітка пры прамым прэсаванні змяншаецца да 5 - 6%. Аднак канструкцыя прэса для зваротнага прасавання складаней, і таму ён радзей ужываецца на практыцы, чым прамой.
Прэсаванне труб вырабляецца звычайна прамым метадам, хоць магчыма прасаванне кароткіх труб вялікага дыяметра (300 - 400 мм) метадам сустрэчнай плыні металу.
Пры прэсаванні труб прамым метадам (мал. IV.17,6) нагрэты злітак пасылаецца ў паражніну кантэйнера 3 прессшайбой 2 шплінтона 1, злёгку цацаўся ў ёй, а затым прашываецца наскрозь сталёвай іголкай 4. Іголка злучана штоком 8 з плунжером гідраўл па восі прэса ззаду галоўнага цыліндру, кіраўніка працоўным ходам прэсшайбы. Пярэдні канец іголкі праходзіць скрозь злітак, высоўваецца на некаторую адлегласць з адтуліны матрыцы 5 і спыняецца. Затым уключаецца галоўны цыліндр прэса, пачынае свой рух прессшайба са шплінтанам, і адбываецца выдушванне металу 7 праз колцавы зазор, адукаваны сценкамі адтуліны матрыцы і вонкавай паверхняй іголкі (мал. IV.17, у). Вонкавы дыяметр атрымоўванай трубы 6 адпавядае, такім чынам, дыяметру адтуліны матрыцы, а ўнутраны - дыяметру іголкі.
Прэсы , якія выкарыстоўваюцца для вырабу пруткоў, профіляў і труб па канструкцыі падзяляюцца на вертыкальныя намаганнем у 300 і 600 т (2,94 і 5,88 МН) і гарызантальныя намаганнем ад 600 да 14 000 т (5,88 да 137,3 МН) . На вертыкальных прэсах атрымліваюць пруткі і танкасценныя трубы дыяметрам да 40 мм і даўжынёй да 3 м; гатовы выраб пры прэсаванні на такіх прэсах выходзіць уніз, у сутарэннае памяшканне. На гарызантальных прэсах атрымліваюць трубы і пруткі вялікіх памераў.
На прэсе 14 000 т (137,3 МН) апроч профіляў з сталым перасекам па даўжыні вырабляюць дэталі ступеністай формы, а таксама рабрыстыя панэлі для самалётаў. Апошнія выціскаюцца спачатку ў выглядзе профіля U-вобразнай або колцавай формы, якія разгортваюцца затым у плоскую панэль на адмысловай машыне. На паказаным прэсе вырабляюцца таксама трубы дыяметрам 500 мм, даўжынёй 15 м пры таўшчыні сценкі ў 6 мм.
Прэсаваннем атрымліваюць і сталёвыя профілі з допускам ±0,4 мм; для атрымання яшчэ большай дакладнасці памераў перасеку яны падвяргаюцца каліброўцы валачэннем.
Па прадукцыйнасці працэс прасавання сталі паспяхова канкуруе з пракаткай, бо месячны выпуск на прэсе 3000 т (29,4 МН) дасягае 8000 т, пры гэтым дакладнасць атрымоўваных прасаваннем вырабаў вышэй, чым пры пракатцы. Галоўнай жа перавагай працэсу прасавання з'яўляецца магчымасць атрымання вельмі складаных профіляў, выраб якіх пракаткай наогул няздзейсна.
§ 13. Сутнасць працэсу валачэння і вобласць яго прымянення
Пры валачэнні, уяўлялым сабой працэс протягивания нарыхтоўкі праз адтуліну ў матрыцы (мал. IV.18), мае месца схема аб'ёмна-напружанага стану з адным галоўным расцягваючым напружаннем σ₁ выкліканым намаганнем валачыльнага табару, і двума іншымі, роўнымі па велічыні галоўным сціскаючым напружанням σ₂ і σ₃, які ствараецца супрацьціскам сценак матрыцы.
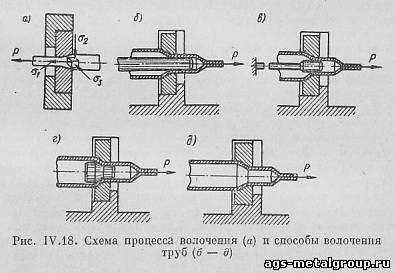
Наяўнасць значнай па велічыні галоўнай расцягвалай напругі σ₁ паніжае пластычнасць металу, абмежаваную да таго ж ўмовамі лядоўні апрацоўкі. Таму пры валачэнні недапушчальныя вялікія ступені дэфармацыі, і за адну протяжку памяншэнне пляца перасеку нарыхтоўкі не перавышае 25 - 35%. Паколькі асноўнай мэтай валачэння з'яўляецца атрыманне тонкага дроту з катанкі дыяметрам 5 - 6 мм, то з прычыны абмежаванасці велічыні абціскання за адну протяжку прыходзіцца працягваць нарыхтоўку паслядоўна праз шэраг паступова якія звужваюцца адтулін матрыц або валок, каб атрымаць патрабаваны канчатковы дыяметр дроту.
Умацаванне (наклеп) металу падчас валачэння выклікае нарастальную страту пластычнасці металу, якая можа прывесці да абрыву дроту. У пазбяганне абрыву дроту напруга нацяжэння ў канцы яе, які выцягваецца з матрыцы, не павінна перавышаць мяжы цякучасці металу. Акрамя таго, для папярэджання абрываў з прычыны наклепа пры шматразовым валачэнні даводзіцца звяртацца да адпалу паўфабрыката. Сумарныя абціскі нарыхтоўкі паміж адпаламі складаюць у сярэднім 75 - 85%.
Валачэннем апрацоўваюць сталі розных марак, а таксама каляровыя металы і іх сплавы.
Валачэнне ўжываецца для атрымання тонкага дрота дыяметрам 0,02 - 1 мм і больш; танкасценных труб, вырабленых папярэдне пракаткай ці прасаваннем; пры каліброўцы гарачакачанага гатункавага пракату дыяметрам да 100 мм; для выраба фасонных профіляў, з якіх шляхам разрэзкі атрымліваюць затым гатовыя дэталі - прызматычныя і сегментныя шпонкі, прызматычныя накіроўвалыя для прыбораў, апорныя прызмы, шлицевые валікі, зубчастыя і храповые колы для гадзіннікавай вытворчасці і т. п.
Апошні выгляд валачэння рэзка скарачае выдатак металу і працаёмкасць вырабу названых дэталяў у параўнанні з апрацоўкай іх на металарэжучых станках з гатункавага пракату.
§ 14. Тэхналогія валачэння
Працэс валачэння складаецца з наступных аперацый:
1) папярэдняга адпалу нарыхтовак для атрымання дробназярністай структуры металу і падвышэнні яго пластычнасці;
2) тручэння іх у летнім растворы сернай кіслаты для выдалення акаліны, якая выклікае падвышаны знос матрыцы;
3) прамыванні нарыхтовак і нейтралізацыі травільнага раствора;
4) завастрэнні канцоў нарыхтовак у ковочных вальцах або пад пнеўматычным молатам для пропуску яго праз адтуліну матрыцы і наступнага захопу абцугамі табара;
5) валачэння;
6) адпалу для ўхілення паклёпу;
7) аздабленні гатовай прадукцыі (абразанні канцоў, праўкі, рэзанні на кавалкі мернай даўжыні і інш.).
Для памяншэння трэння ў ачку матрыцы валачэнне вырабляецца са змазкай нарыхтоўкі мінеральнымі алеямі, эмульсіяй, графітам або жывёламі тлушчамі. Змазка спрыяе атрыманню чыстай паверхні выраба і памяншае выдатак энергіі на валачэнне. Для зніжэння намагання валачэння ўжываюць таксама ролікавыя матрыцы.
У шэрагу выпадкаў, напрыклад перад валачэннем дроту і танкасценных труб са сталі, вырабляюць іх амедненне апусканнем нарыхтовак у слабы кіслотны раствор меднага купарваса; омеднение зніжае каэфіцыент трэння і засцерагае паверхню выраба ад задзірання ў ачку матрыцы.
Валачэнне труб вырабляецца наступнымі асноўнымі спосабамі: на доўгай апраўцы (мал. IV.18, бы), калі труба працягваецца разам з апраўкай праз нерухомую матрыцу; на нерухомай кароткай апраўцы (мал. IV.18, в); на вольнай (якая плавае) апраўцы (мал. IV.18,г) - разнавіднасць валачэння на кароткай апраўцы; без апраўкі (мал. IV.18, д). Каэфіцыент выцяжкі за адзін праход звычайна не перавышае 1,5 - 1,8.
Валачыльныя станы па спосабе ажыццяўлення цягнучага намаганні дзеляцца на ланцужныя і барабанныя. У ланцужных станах(мал. IV.19, а), ужывальных для валачэння пруткоў, профіляў і труб даўжынёй 8 - 10 м, высілак валачэння ствараецца бясконцым шарнірным ланцугом 6, за звёны якой зачэпліваецца крук 5 валачыльнай карэткі 4. Карэтка мае самозахватывающие абцугі 3, з дапамогай якіх матэрыял 2 працягваецца скрозь матрыцу 7, прымацаваную да кранштэйна 8 станіны 1; карэтка забяспечаная чатырма ролікамі, для перасоўвання па накіроўвалых станіны 1. Рухаючыся разам з ланцугом, карэтка захапляе за сабой захоплены абцугамі пруток 2. Зварот карэткі, пасля протягивания штангі на ўсю даўжыню, вырабляецца ўручную ці адмысловай прыладай. Шарнірны ланцуг атрымлівае рух ад электраматора з рэдуктарам праз вядучую зорачку. Ланцужныя валачыльныя постаці вырабляюцца з высілкам цягі 1 - 150 т (9,81-147,2 кн), што дазваляе працягваць пруткі з пачатковым дыяметрам да 150 мм і трубы дыяметрам да 200 мм. Хуткасць валачэння на іх можа дасягаць 50 м/мін. Лік адначасова протягиваемых пруткоў у постацях новай канструкцыі можа дасягаць 10.
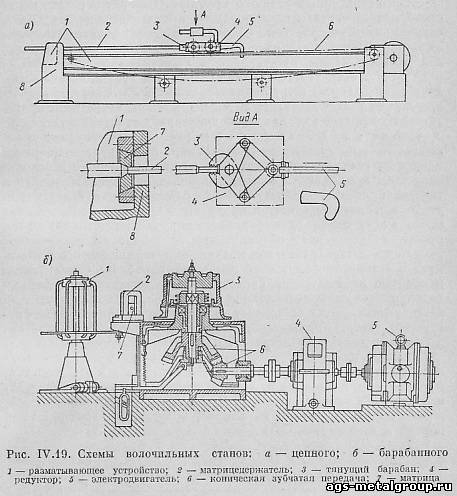
У барабанных станах(мал. IV.19,6) высілак валачэння ствараецца які верціцца барабанам, на якім з дапамогай клешчавога захопу замацоўваецца канец працягванага дрота. Гэтыя постаці ўжываюцца звычайна для валачэння доўгага тонкага і тоўстага дрота дыяметрам 0,02-6 мм і пруткоў дыяметрам да 16 мм, намотваемых у бухту на кіроўны барабан. Такія станы могуць мець адзін барабан для аднаразовага валачэння дроту праз адну матрыцу, або некалькі паслядоўна размешчаных барабанаў і матрыц для шматразовага валачэння. У станах шматразовага валачэння дрот намотваецца цалкам на апошні барабан, на прамежкавыя барабаны намотваецца толькі некалькі віткоў дроту, якая адначасова змотваецца з адной часткі барабана і намотваецца на іншую яго частку. Дыяметры барабанаў складаюць 150 - 1000 мм, а хуткасць валачэння дасягае 2000 м/мін і больш.
Інструментам для валачэння служаць матрыцы - валокі або фільеры, валачыльныя дошкі, кольцы і апраўкі . Яны вырабляюцца з інструментальных сталей і цвёрдых сплаваў. Пры валачэнні найтонкага дроту ўжываюць валокі з дыямента, якія валодаюць высокай цвёрдасцю і ўстойлівасцю.
|