СПЕЦЫЯЛЬНЫЯ ПРАЦЭСЫ АПРАЦОЎКІ МЕТАЛАЎ ЦІСКАМ
33. Апрацоўка ліставога металу
Да спецыяльных працэсаў апрацоўкі ціскам ліставых нарыхтовак адносяцца вальцоўка цыліндрычных абечак, такарна-ціскальныя работы, атрыманне гнутых профіляў з ліста і стужкі.
Вальцоўку цыліндраў-обечаек з ліста таўшчынёй 4 - 60 мм, ужывальных у зварных металаканструкцыях (калоны, трубы, катлы і т. п.), выконваюць гнуткай па патрабаваным радыусе на трохвалковых вальцах. Такія вальцы маюць верхні халасты валок большага дыяметра і два прывадных ніжніх валка (мал. 47, а), якія верцяцца электрарухавіком праз рэдуктар. Даўжыня валкоў у магутных вальцоў дасягае 6 - 8 м, а дыяметр 400 - 600 мм, што дазваляе вальцаваць абечак значных габарытаў.
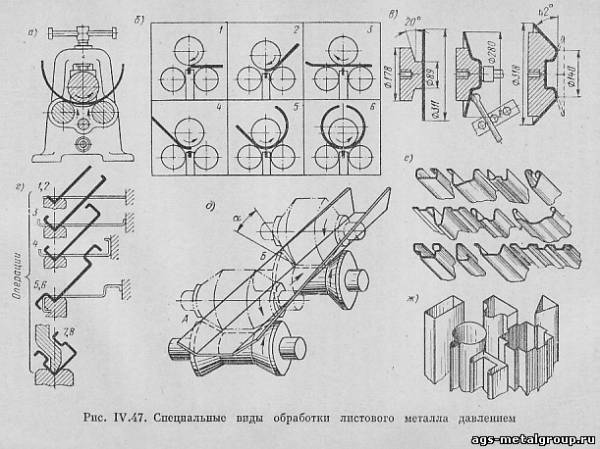
Пры вальцоўцы плоскую загатоўку з прагабляванымі на кромкострогальном станку фаскамі пад зварку ўводзяць у вальцы (мал. 47, бы, 1) і некалькі падгінаюць адзін яе бок (2, 3).
Затым аналагічна падгінаюць іншы яе бок (4) і пасля гэтага канчаткова вальцуюць абечак (5, 6). Перасоўванне выгінальнага ліста паміж валкамі адбываецца пад дзеяннем сіл трэння. Крывізна атрымоўванага выраба залежыць ад узаемнага становішча верхняга і ніжняга валкоў і можа змяняцца пры ўздыме ці апусканні верхняга валка націскнымі шрубамі. Вальцаваннем можна атрымліваць таксама конусныя абечакі і колцавыя дэталі з паласы, кутняй сталі і т. п.
Формаўтварэнне вырабаў на такарна-давільных станках (ратацыйнае выдушванне) выконваецца ў тых выпадках, калі штампоўка іх эканамічна невыгодная (дробнасерыйная вытворчасць, вялікія памеры або складаны контур дэталяў). Пры ратацыйным выдушванні ліставую нарыхтоўку (гурток) дэфармуюць абцісканнем яе на якая верціцца апраўцы ролікамі або цвёрдым стрыжневым ціскавіком з шаравой галоўкай (мал. 47, у). Ратацыйнае выдушванне можа выконвацца без утанения сценак і з зададзеным утонением. Нарыхтоўкі дэфармуюць звычайна ў халодным стане, пры гэтым утонение сценкі за 2 - 3 праходу можа дасягаць 90%. Хуткасць выдушвання можа дасягаць 300 м/мін, падачы - ад 0,25 да 2,5 мм на абарачэнне шпіндзеля. Дакладнасць памераў вырабаў высокая і ляжыць у межах: па таўшчыні сценкі ад ± 0,05 да ± 0,03 мм і па дыяметры ад ± 0,15 да ± 0,03 мм. Дыяметры апрацоўваных сталёвых полых вырабаў дасягаюць 3 м пры пачатковай таўшчыні сценкі 25 мм. Для змазкі давільнага роліка пры высокіх удзельных цісках, якія дасягаюць 28 т/см² ужываюць пасту з дисульфата малібдэна або цынкавую завісь.
Развальцоўку канцоў у трубавых дошках цеплаабменных апаратаў вырабляюць сталёвым загартаваным ролікам, якія атрымліваюць кручэнне ад пнеўмамашынкі ці пераноснага электрарухавіка, а таксама запрэсоўкай выбухам. Гнутыя профілі даўжынёй да 2 - 3 м атрымліваюць паслядоўнай лядоўні гнуткай кутоў ліставай нарыхтоўкі (мал. 47, г) штампам, якія складаюцца з пуансона і матрыцы на адмысловых гнуткавых прэсах. Пры большай даўжыні ліставыя профілі (мал. 47, е) атрымліваюць больш прадукцыйным працэсам - прафіляваннем сталёвай стужкі фасоннымі ролікамі на роліка-гнуткавых станках (мал. 47, д). Гэтыя станы бесперапыннага дзеяння ўяўляюць сабой шэраг паслядоўна размешчаных клетак з парамі прывадных ролікаў, якія ажыццяўляюцца паступова змена формы папярочнага перасеку профилируемой стужкі без патанення яе сценак. На мал. 47, д паказаны працэс прафілявання пры праходжанні нарыхтоўкі праз дзве сумежныя пары ролікаў (верхнія ролікі намаляваны штрыхавымі лініямі). На другой пары ролікаў адбываецца падгін сценак профіля на вугал α. Змена кута адбываецца паступова на ўчастку даўжыні профіля АБ. Велічыня кута подгибки пры пераходзе ад першай пары ролікаў да наступных паступова памяншаецца з прычыны нарастальнага наклепа металу.
Пасля прафілявання ў роліках паўфабрыкаты нярэдка зварваюць па даўжыні кантактнай шовной зваркай з мэтай атрымання цвёрдых замкнёных профіляў коробчатого, цыліндрычнага і іншых перасекаў (мал. 47, ж).
Танкасценныя гнутыя профілі з таўшчынёй сценкі 0,5 мм і больш валодаюць высокай трываласцю і калянасцю пры невялікай вазе. Замяняючы цяжэйшы гарачакачаны пракат (швелеры, зетавы і іншыя профілі), яны з'яўляюцца прагрэсіўным матэрыялам для металічных канструкцый.
§ 34. Прафіляванне фасонных паверхняў накатваннем
Метад формаўтварэння вонкавых фасонных паверхняў цыліндрычных дэталяў шляхам накатвання іх якая верціцца прыладай у халодным стане наўзамен апрацоўкі іх рэзаннем атрымаў значнае распаўсюджванне. Ён шырока ўжываецца для накаткі разьбярстваў, дробнашліцавых валаў, рыфленняў, таўроў і маломодульных зубчастых колаў. Да пераваг накатвання перад апрацоўкай са здыманнем стружкі ставяцца высокая прадукцыйнасць (напрыклад, пры накатванні разьбы плашкамі яна ў 16 разоў вышэй, чым пры наразанні яе леркамі), нізкі кошт апрацоўкі, эканомія металу і нараўне з гэтым падвышэнне механічнай і стомленай трываласці дэталяў. Больш высокая трываласць і зносаўстойлівасць накатаных дэталяў абумоўлена тым, што валакна металу пры формаўтварэнні, напрыклад зуб'яў шасцерняў, пластычным дэфармаваннем не пераразаюцца, а ўціскаюцца;
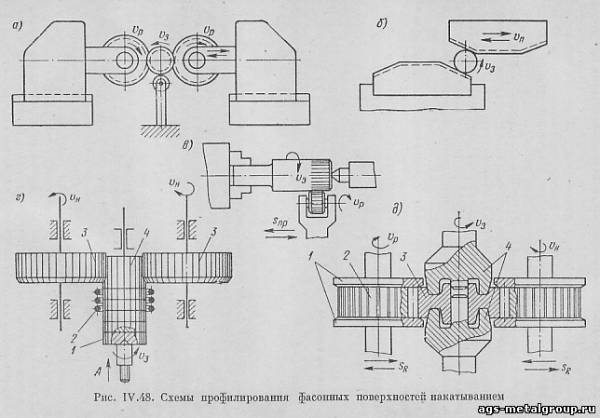
Накатванне разьбярстваў выконваецца шрубавымі і колцавымі ролікамі (мал. 48, а) або плоскімі плашкамі (мал. 48, бы) на разьбанакатных станках, якія развіваюць высілак да 25 т (246 кн). Шрубавыя разьбанакатныя ролікі маюць шматзаходнае разьбярства з кірункам уздыму процілеглым накатываемой нітцы. Датыкаючыся з нарыхтоўкай па ўсёй даўжыні накаткі яны паступова ўціскаюцца ў яе дзякуючы радыяльнай падачы, утворачы профіль разьбы. На ролікавых разьбанакатных станках, якія працуюць па схеме папярочнай пракаткі, накатваюць разьбы дыяметрам да 120 мм, з крокам да 6 мм, пры гэтым даўжыня накатываемой разьбы абмежаваная шырынёй разьбанакатных шрубавых ролікаў (150 мм).
Доўгія (да 1200 мм) трапецыяпадобныя і іншыя спецыяльныя разьбы з буйным крокам (да 8 мм) выконваюцца папярочна-шрубавай накаткай двума ролікамі шырынёй да 100 мм з колцавым разьбовым або шрубавым разьбовым профілем на станках канструкцыі ЦНИИТмаша; пры гэтым прадукцыйнасць бесперапыннага накатвання надзвычай высокая. Накатванне дробнашліцавых паверхняў і рыфленняў на валіках і дзяржальнях выконваецца на звычайных такарна-вінтарэзных станках (мал. 48, у) пасродкам загартаваных ролікаў-накатнікаў вольна якія верцяцца на восі дзяржальні, замацаванай на суппорце станка.
Накатванне зуб'яў сталёвых шасцерняў вырабляюць на зубанакатных станах у халодным стане да модуля 1 - 2 мм і з нагрэвам нарыхтовак ТВЧ да модуля 10 мм і больш. Накатваецца як прамы, так і спіральны зуб на цыліндрычных і канічных шасцярнях. Шасцярні невялікага дыяметра, да 250 мм, з модулем да 3 мм накатваюць прутковым спосабам на табары канструкцыі ЦНИИТмаша двума накатнымі валкамі са сталі 5ХНВ (мал. 48, г). Нарыхтоўка 1 у выглядзе суцэльнага цыліндру або набору асобных дыскаў усталёўваецца ў цэнтрах суппорта табара так, каб кантавая частка верхняй нарыхтоўкі знаходзілася на ўзроўні колцавага награвальнага індуктара 2, размешчанага пад працоўнымі зубчастымі валкамі 3. Нарыхтоўка атрымлівае кручэнне ад дзялільнай шасцярні 4, валкамі. Пры ўключэнні індуктара т. ст. г. верхні канец якая верціцца нарыхтоўкі награваецца да 1100 - 1150' З, пасля чаго ўключаецца механізм восевай падачы і нарыхтоўка пачынае перамяшчацца ўверх (па стрэлцы А). Профіль зуба пасля накатвання дадаткова не апрацоўваецца. Час пракаткі адной шасцярні складае 9 - 20 сек, замест 8 мін фрэзеравання зуб'яў такой шасцярні на зубафрэзерным станку.
Буйныя шасцярні, дыяметрам да 600 мм з модулем да 10 мм, накатваюць адзінкавым спосабам (мал. 48 д) на постаці ЦБКММ-13. Нарыхтоўка 3 перад накатваннем заціскаецца ў апорных конусах 4 ніжняга прываднага стала суппорта і верхняй рухомай галоўкі і награваецца сектарным індуктарам, усталяваным ззаду, паміж валкамі-накатнікамі 2, забяспечанымі абмежавальнымі дыскамі 1. Затым нарыхтоўцы і валкам паведамляецца ўзгодненае кручэнне , дэфармуючы нагрэтую паверхню нарыхтоўкі, утвораць на ёй зуб'і эвальвентнага профіля. Час накатвання зуб'яў адной шасцярні, па дадзеных ЧТЗ, складае 3,5 мін, эканомія металу на 1 шт. - 1,5 кг.
Пасля накаткі прадугледжваецца чыставое фрэзераванне зуб'яў.
§ 35. Аздобная і ўмацавальная апрацоўка дэталей
У наш час у машынабудаванні ўсё гушчару сталі ўжываць чыставую апрацоўку дэталяў шляхам пластычнага дэфармавання павярхоўнага пласта металу. Асноўнымі відамі такой апрацоўкі (мал. 49) з'яўляюцца: пракочванне паміж ролікамі (а), абкочванне цыліндрычных знешніх (б), унутраных (у) або плоскіх (г) металічных паверхняў свабодна верцяцца ролікамі або шарыкамі, выгладжванне (дарнаванне) адтулін працягваннем або праштурхваннем некруцільнай прылады дарна (д), калібраванне адтулін праштурхваннем шарыка (е). У выніку халоднай пластычнай дэфармацыі пры абкатцы або дарнаванні з'яўляецца наклеп павярхоўнага пласта металу, змяняецца яго структура і цвёрдасць. Пры гэтым змяняюцца выступы ад папярэдняй паўчыставай або чыставой апрацоўкі рэжучай прыладай, запаўняюцца западзіны і рыскі,
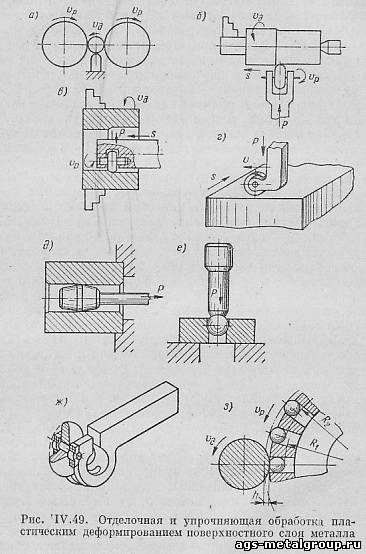
Павярхоўная ўмацавальная апрацоўка павялічвае стомленую трываласць дэталяў на 50 - 100%, а зносаўстойлівасць і тэрмін службы дэталяў у некалькі разоў. Абкаткай ролікамі і шарыкамі ўмацоўваюць шыйкі і працоўныя паверхні пракатных валкоў, штокаў штамповачных молатаў, хваставікі канатных барабанаў вугальных камбайнаў, шыйкі каленчатых валаў і іншыя адказныя дэталі. Абкочванне профільнымі ролікамі ўжываюць для ўмацавання складаных паверхняў, напрыклад западзін паміж зуб'ямі шасцерняў і віткамі буйнамодульных чарвячных разьбярстваў.
Для абкатвання і раскочванні вонкавых і ўнутраных паверхняў ужываюць аднаролікавыя (аднашарыкавыя) (мал. 49, ж) або шматролікавыя прынады - накаткі, у якіх высілак на ролік ствараецца магутнымі спружынамі ці пнеўмагідраўлічнымі прыладамі, а таксама шарыкавыя ўмацавальнікі. У апошніх для наклепа паверхні дэталі выкарыстоўваецца цэнтрабежная сіла шарыкаў, вольна якія сядзяць у адтулінах дыска-ўмацавальніка, хутка які верціцца на шпіндзелі прынады (мал. 49, з). Накатка усталёўваецца звычайна ў суппорце такарнага станка. Па сваёй прадукцыйнасці халодная аздобная апрацоўка не саступае шліфаванню і суцэль замяняе яго.
§ 36. Тэхніка бяспекі пры апрацоўцы металаў ціскам
У сувязі з выкарыстаннем магутнага высокапрадукцыйнага абсталявання з часткамі, якія верцяцца і рухаюцца зваротна-паступальна, у тым ліку машын ударнага дзеяння, а таксама наяўнасцю транспартных патокаў гарачага металу ўзрастае верагоднасць атрымання траўм работнікамі цэхаў.
У мэтах папярэджання вытворчага траўматызму праводзяцца мерапрыемствы па ахове працы і тэхніцы бяспекі ў цэхах гарачай і лядоўні апрацоўкі металаў ціскам. У гэтых цэхах забяспечваюцца інтэнсіўная вентыляцыя, агароджа небяспечных зон і падвышаная асветленасць, вырабляецца ўзмоцнены інструктаж аб метадах бяспечнай працы для ўсіх, хто паступае на працу і пры пуску ў эксплуатацыю новага абсталявання. Асноўныя патрабаванні бяспечнай працы ў названых цэхах зводзяцца да наступнага.
Не дапушчаецца праца з гарачым металам без рукавіц, з няспраўнымі і непрыдатнымі па профілі металу абцугамі. Пры разагрэве печаў, якія працуюць на мазуце і газе, спачатку ў фарсункі (гарэлкі) падаецца паветра, а затым асцярожна ўключаецца падача паліва; пры прыпынку печаў, наадварот, перш выключаецца падача мазуту або газу, а затым паветра.
У пракатных цэхах не дазваляецца працірка і чыстка валкоў пракатных табараў і лістаправільных машын са боку ўваходу металу. Для перадачы дробнасортнага пракату і дроту з калібра ў калібр пры лінейным і паўбесперапынным размяшчэнні клетак табара павінны быць змантаваны праводкі - жолабы, надзейна накіравальныя метал. Ральгангі і іншыя месцы транспарціроўкі пракату, які ідзе з вялікай хуткасцю пры выхадзе з апошніх клетак, павінны быць надзейна агароджаны і абсталяваны металічнымі пераходнымі масткамі і трапамі з поручнямі.
У трубапрэсавых цэхах асноўная ўвага звяртаецца на добры стан гідраўлічнай сістэмы, якая працуе пад высокім ціскам, і правільную яе эксплуатацыю. Месцы выхаду з матрыц прэсаваных пруткоў і труб павінны быць надзейна агароджаны з прычыны вялікай хуткасці заканчэння металу.
Пры працы на валачыльных постацях не дазваляецца разблытваць дрот падчас валачэння, без прыпынку агрэгата. Барабаны станаў агароджваюць шчытамі, якія засцерагаюць працоўных ад удараў канцом дроту, якія выходзяць з валокі, або пры яе абрыве. Падчас запраўкі станаў шматразовага валачэння неабходна сачыць, каб пальцы не патрапілі паміж дротам і цягавай шайбай; запраўляць табар можна толькі на невялікай хуткасці.
У кавальскіх цэхах забараняецца ўжываць для кавання байкі, кавадлы і іншая прылада з расколінамі і празмеру зношанымі працоўнымі паверхнямі. Нарыхтоўку варта трымаць у абцугах трывала двума рукамі, накіроўваючы ручкі абцугоў у бок ад сябе, каб не атрымаць удару ў жывот ці нагу. Пакоўка і падкладныя штампы павінны размяшчацца ў цэнтры байка молата. Перакос плоскасцяў байкоў не дапушчаецца. Кліны, якія мацуюць байкі і штампы на молатах, павінны быць надзейна забітыя, іх канцы не павінны выступаць. Для папярэджання выпадковых уключэнняў прэсаў і нажніц уладкоўваюцца ахоўныя шчыткі над педалямі. Пры высечцы, гнутцы, выцяжцы і іншых аперацыях ліставай штампоўкі рукі працавальнага не павінны знаходзіцца ў небяспечнай зоне паміж пуансонам і матрыцай. Для папярэджання траплення рук у штамп ужываюцца аўтаматычныя сеткаватыя агароджы небяспечнай зоны, якія апускаюцца пры ходзе паўзуна ўніз, рукоустранители, якія адводзяць рукі пры апусканні пуансона, і сістэмы двухручнага ўключэння прэса. Пры такой сістэме прэс можа зрабіць працоўны ход толькі пры адначасовым націску на якія адпавядаюць рычагі двума рукамі. Найбольш надзейным мерапрыемствам для засцярогі рук ад пашкоджання з'яўляецца аўтаматычная падача матэрыялу.
|