§ 15. Сутнасць працэсу і віды кавання
Пры коўцы металу паміж плоскімі байкамі мае месца свабодная плынь яго ў бакі, таму такое каванне атрымала назву свабоднай.
Вольная коўка эканамічна выгодная пры атрыманні фасонных нарыхтовак сталёвых дэталяў з высокімі механічнымі ўласцівасцямі ва ўмовах індывідуальнай і дробнасерыйнай вытворчасці.
Да пераваг кавання ў параўнанні з іншымі спосабамі апрацоўкі металаў, напрыклад ліццём, рэзаннем, штампоўкай, ставяцца: яе ўніверсальнасць у стаўленні вагі, формы і памераў партыі изготовляемых нарыхтовак; забеспячэнне высокіх механічных уласцівасцяў металу ў вырабах, адсутнасць выдаткаў на дарагое тэхналагічнае абсталяванне; магчымасць выкарыстання параўнальна маламагутных машын - прылад дзякуючы канцэнтраванаму з дадаткам намаганняў кавання ў абмежаваным байкамі невялікім аб'ёме дэфармуемага металу.
У прамысловасці вольная коўка ўжываецца для выраба паковак шасцерняў, турбінных ротараў і дыскаў, валаў, шатуноў, кольцаў і іншых адказных дэталяў машын. Вольная коўка з'яўляецца пакуль незаменнай у вытворчасці буйных дэталяў, нягледзячы на шэраг уласцівых ёй недахопаў. Да іх ставяцца, напрыклад, параўнальна нізкая прадукцыйнасць працы і невялікая дакладнасць кавання, якая выклікае неабходнасць значных прыпускаў і напускаў металу, што прыводзіць да падвышэння выдатку матэрыялу і кошты гатовых дэталяў.
Вольная коўка падзяляецца на ручную і машынную.. Ручное коўка ўжываецца рэдка, галоўнай выявай у рамонтных майстэрнях пры вырабе невялікіх паковак і амаль не мае прамысловага ўжывання на заводах. Машынная коўка вырабляецца на ковочных молата і прэсах. На молатах вырабляюць пакоўкі масай ад 0,5 да 100 кг, выкарыстаючы ў якасці зыходнага матэрыялу гатункавы пракат перасекам да 250х250 мм і абціснутую даўбешку (блюмсы) перасекам да 450Х450 мм. На гідраўлічных ковочных прэсах вырабляюць пакоўкі масай ад 100 кг да 230 т, са сталёвых зліткаў масай ад 1,2 да 350 т.
§ 16. Асноўныя аперацыі тэхналагічнага працэсу кавання і прыёмы іх выканання
Тэхналагічны працэс машыннага вольнага кавання складаецца з шэрагу элементарных кавальскіх аперацый, выкананых у вызначанай паслядоўнасці з мэтай атрымання з зыходнай нарыхтоўкі простай формы (злітка, блюмса) фасоннага пакавання патрабаваных памераў і формы.
Акрамя чыста кавальскіх аперацый поўны тэхналагічны працэс выраба пакоўкі, які фіксуецца ў адмысловай тэхналагічнай карце, уключае таксама нарыхтоўчыя аперацыі (рэзку або рубку нарыхтовак і іх кантроль), нагрэў металу пад коўку, астуджэнне паковак, кантрольныя аперацыі па праверцы памераў і механічных уласцівасцяў пакоўкі (калі гэта патрабуецца тэхнічнымі ўмовамі), а таксама аперацыі першаснай тэрмічнай апрацоўкі паковак (адпал, нармалізацыю), якія выконваюцца звычайна ў кавальскім цэху.
Асноўнымі аперацыямі працэсу вольнага кавання з'яўляюцца ўляганне, выцяжка, прашыўка, гнуткая, рубка. Да меней распаўсюджаным кавальскім аперацыям ставяцца перадача металу, закручванне і кавальская зварка. Акрамя пералічаных аперацый падчас вырабаў паковак ужываюцца і іх разнавіднасці: высадка ў падкладных кольцах, уяўлялая сабой частковае ўляганне нарыхтоўкі па яе вышыні; абкатка па дыяметры (пасля ападкі), выцяжка і раздача колцавых паковак на апраўцы. У шэрагу выпадкаў тэхналагічны працэс кавання ўключае аперацыі гарачай штампоўкі ў падкладных штампах пад молатам.
Наяўнасць тых ці іншых кавальскіх аперацый, а таксама парадак іх чаргавання вызначаюцца формай изготовляемой пакоўкі. Так, напрыклад, пры вырабе паковак тыпу валаў ужываюцца галоўнай выявай выцяжка і рубка, а ў выпадку кавання каленчатых валаў выцяжка і перадача металу. Пры вырабе колцавых паковак ужываюць уляганне, прашыўку, раздачу, а часам і выцяжку на апраўцы. Для кавання фланцавых паковак характэрны высадка, прашыўка, абкатка па дыяметры.
Пры машынным каванні нарыхтоўка ўкладваецца на ніжні нерухомы баек молата або прэса, а затым дэфармуецца або непасрэдна верхнім рухомым байком або з ужываннем падкладной прылады, які змяшчаецца паміж верхнім байком і нарыхтоўкай.
Бойкібываюць плоскімі і выразнымі (мал. IV.20, а). Выразныя байкі выкарыстоўваюць пры каванні валаў, іх ужыванне паскарае працэс кавання і павялічвае пластычнасць металу падчас дэфармацыі.
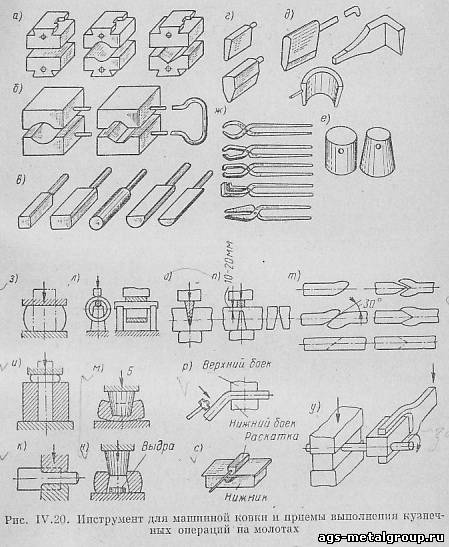
Падкладнымі прыладамі служаць: абцісканні (мал. IV.20, бы) для аздаблення цыліндрычных і кантаваных паверхняў пасля папярэдняй выцяжкі паковак на плоскіх байках; раскочванні (мал. IV.20, у) для мясцовай дэфармацыі металу, напрыклад пры каванні аднабаковых уступаў; пераціскання (мал. IV.20, г) для разметкі матэрыялу пры каванні і пераціску металу нарыхтоўкі на аб'ёмы, якія ідуць на адукацыю асобных частак пакоўкі; тонары (мал. IV.20, д) і квадраты для рубкі металу; прашыўні (мал. IV.20, е) для прабіўкі адтулін; апраўкі для каліброўкі прашытых адтулін; апраўкі для раздачы адтулін і выцяжкі пустотелых паковак (мал. IV.20, л).
Для пераносу, падтрыманні, падачы і кантоўкі невялікіх нарыхтовак карыстаюцца абцугамірозных канструкцый і памераў (мал. IV.20, ж). Пры каванні буйных паковак для гэтай мэты выкарыстоўваюць найпростыя прынады: самазаціскныя абцугі, воротяжки, відэльцы , якія падвешваюцца на ланцужным блоку кансольна-паваротных кранаў, усталёўваных у молатаў, а таксама механічныя кантавальнікі і маніпулятары падвеснага і падлогавага тыпаў.
Пры ўляганнінарыхтоўка ўсталёўваецца вертыкальна на ніжні баек молата (мал. IV.20, з) і дэфармуецца ўдарамі верхняга байка па тарцы нарыхтоўкі. Ападка выклікае павелічэнне папярочнага перасеку нарыхтоўкі за рахунак памяншэння яе вышыні. У пазбяганне падоўжнага выгібу даўжыня якая абсякаецца нарыхтоўкі не павінна перавышаць 2,5 яе дыяметра. Разнавіднасцю ападкі з'яўляецца высадка, якая ўяўляе сабой частковае ўляганне нарыхтоўкі па вышыні (мал. IV.20, і). Пры высадцы нарыхтоўку ўсталёўваюць у сталёвае падкладное кольца на байцы молата і дэфармуюць толькі верхнюю вольную частку нарыхтоўкі.
Пры выцяжцы(мал. IV.20, да) нарыхтоўка ўкладваецца плазам папярок байкоў молата і дэфармуецца паслядоўнымі абцісканнямі. Пасля кожнага ўдару нарыхтоўка кантуецца т. е. паварочваецца на 90° вакол падоўжнай восі, і падаецца наперад у кірунку выцяжкі. Выцяжка выклікае павелічэнне даўжыні нарыхтоўкі за рахунак памяншэння пляца яе папярочнага перасеку.
Пры вырабе колцавых паковак з адтулінамі вялікага дыяметра ўжываюць раздачу (раскочванне) кольцаў на апраўцы (мал. IV.20, л), якая ўяўляе сабой прыватны выпадак выцяжкі. Пры раздачы павялічваюцца вонкавы і ўнутраны дыяметры пакоўкі за рахунак памяншэння таўшчыні яе вобада. Пакоўку пасля кожнага ўдару молата паварочваюць на невялікі кут абцугамі вакол сталёвай апраўкі, усталяванай на апорных стойках (клямары) на ніжнім байку молата.
Прашыўка- аперацыя, з дапамогай якой у нарыхтоўках атрымліваюць скразныя адтуліны. Адыход металу пры прашыўцы называецца выдрай. Ужываюць два спосабу прашыўкі: з ужываннем падкладнога кольца і прашыўку з двух бакоў, з пераварочваннем пакоўкі.
Пры прашыўцы на кольцыабложаная нарыхтоўка, звычайна невялікай таўшчыні, укладваецца на сталёвым кольцы, змешчаным на ніжнім байку молата. У цэнтры нарыхтоўкі ўсталёўваецца конусны прашывень, шырокай падставай уніз, які затым укараняецца ў нарыхтоўку спачатку лёгкімі, а затым моцнымі ўдарамі верхняга байка. Пры гэтым метал спачатку выціскаецца з-пад прашыўня ў бакі, а затым адбываецца зрэз яго па цыліндрычнай паверхні, з адукацыяй выдры, якая правальваецца ўніз пад ціскам прашыўня. Пры гэтым спосабе прашыўкі аб'ём металу выдры складае каля 3/4 аб'ёму атрымоўванай адтуліны.
Пры прашыўцы з двух бакоў, ужывальнай для паковак вялікай таўшчыні, нарыхтоўку ўкладваюць непасрэдна на баек молата, усталёўваюць на ёй конусны прашывень, вузкай падставай уніз (мал, IV.20. л) і лёгкімі ўдарамі верхняга байка па прашыўні вырабляюць глухую прашыўку прыкладна на 3/4 вышыні нарыхтоўкі. Затым прошивень выдаляюць абцугамі або ўдарамі па тыльным боку пакоўкі, пакладзенай на кольца, і, усталяваўшы пакаванне на баек глухой адтулінай уніз, вырабляюць скразную прашыўку яе са зваротнага боку (мал. IV. 20, і). Выдра атрымліваецца невялікай вышыні і па аб'ёме складае каля 1/4 аб'ёму якая прашываецца адтуліны.
Рубка металутаксама вырабляецца двума прыёмамі: спачатку нагрэтая нарыхтоўка надсякаецца кавальскай сякерай з аднаго боку (мал. IV.20, аб), а затым пераварочваецца на 180' і рассякаецца канчаткова сталёвым прутком квадратнага перасеку - квадратам (мал. IV.20, п).
Гнутку пры вырабе адзінкавых паковак выконваюць ударамі кавадлы па канцы нарыхтоўкі, заціснутай паміж байкамі молата (мал. IV.20, р). Пры вырабе партыі аднолькавых паковак гнуткую ажыццяўляюць у ніжніку (подкладном штампе) з ужываннем вяршніка ці раскочвання (мал. IV.20, с).
Для закручвання кален пакоўкі вала адно калена заціскаюць байкамі молата, а на іншае апранаюць масіўны відэлец, канец якой павольна паварочваюць (мал. IV.20, у).
Кавальская зварка(мал. IV. 20, т) амаль цалкам выцесненая больш дасканалымі спосабамі электрычнай і газавай зваркі.
§ 17. Распрацоўка чарцяжа пакоўкі
Чарцёж пакоўкі з'яўляецца асноўным тэхналагічным дакументам для кавальскага цэха. Па ім вырабляецца выраб і прыёмка гатовага пакавання. Чарцёж пакоўкі распрацоўваецца па чарцяжы гатовай (апрацаванай на станках) дэталі і ўяўляе сабой графічны малюнак пакоўкі, выкананае ў вызначаным маштабе з указаннем усіх памераў неабходных для яе выраба.
Пакоўка адрозніваецца ад гатовай дэталі наяўнасцю прыпускаў на механічную апрацоўку і напускаў металу.
Напускамметалу называецца мясцовае павелічэнне прыпуску, якое спрашчае канфігурацыю пакоўкі з прычыны немагчымасці або нерэнтабельнасці яе выраба ў адпаведнасці з дакладнай формай дэталі. Напускамі металу перакрываюцца адтуліны невялікага дыяметра, невялікія па вышыні ўступы на валах, пазы, праточкі і т. п.
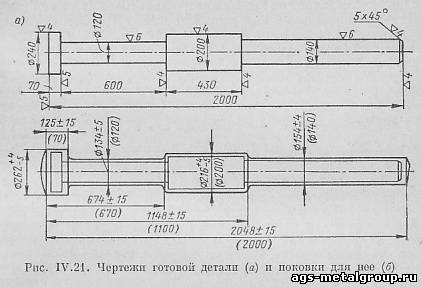
Велічыня припуска залежыць ад складанасці формы і габарытных памераў дэталі і ўлічвае дэфекты вонкавага пласта металу (акаліну, увагнутасці ад націскаў кавальскай прылады, обезуглероживание паверхні), якія павінны быць выдалены пры апрацоўцы рэзаннем для атрымання неабходнай чысціні паверхні і дакладных памераў дэталі.
Намінальныя (акругленыя) памеры пакоўкі з улікам прыпускаў і напускаў металу прастаўляюцца над памернымі лініямі на чарцяжы пакоўкі. Пад размернымі лініямі, у дужках, прастаўляюцца памеры гатовай дэталі.
На чарцяжы пакоўкі паказваюцца таксама дапушчальныя лімітавыя адхіленні ад намінальных памераў пакоўкі са знакамі плюс і мінус, якія ўлічваюць магчымую дакладнасць кавання на молаце ці прэсе.
Прыпускі і допускі на тыпавыя пакоўкі (пласціны, валы кольца і т. п.), изготовляемые коўкай на гідраўлічных прэсах і молатах, выбіраюцца па табліцах ДАСТаў 7062 - 67 і 7829 - 70. Велічыні прыпускаў па дыяметры для буйных прэсавых пакоў 1 да 20 м складае 16 -55 мм на бок, а велічыні гранічных адхіленняў ад ±6 да ±18 мм. Прыпускі па дыяметры для паковак гладкіх валаў даўжынёй 250 - 2500 мм; изготовляемых на молатах, складаюць 5 - 18 мм, а гранічныя адхіленні ад ±2 да ± 5 мм адпаведна.
Прыклад чарцяжа пакоўкі вала з уступамі, які вырабляецца коўкай на молаце, прыведзены на мал. IV.21.
§ 18. Абсталяванне для свабоднага кавання
Абсталяванне кавальскіх цэхаў дзеліцца на асноўнае і дапаможнае.
Да асноўнага абсталявання, Які выконвае дэфармацыю металу пры каванні, ставяцца молаты і прэсы.
Да дапаможнага абсталявання ставяцца машыны для рэзання нарыхтовак - прэс-нажніцы, дыскавыя пілы; награвальныя печы; механізмы, якія транспартуюць і падтрымліваюць нарыхтоўкі пры каванні - ковочные пад'ёмныя краны, кантавальнікі, маніпулятары.
Асноўнае кавальскае абсталяванне адрозніваецца па хуткасці працоўнага ходу , т. е. ходу, на працягу якога вырабляецца дэфармаванне пакоўкі. Хуткасць байка молата да моманту ўдару па нарыхтоўцы значная і дасягае 7 - 8 м/сек; наступная дэфармацыя металу ажыццяўляецца за кошт кінэтычнай энергіі, назапашанай цяжкімі падаючымі часткамі (поршнем, штоком, бабай і верхнім байком) да моманту ўдару байка аб нарыхтоўку. Таму гавораць, штомолаты - гэта машыны дынамічнага дзеяння, якія працуюць ударам. Ковачныя гідраўлічныя прэсы дэфармуюць метал значным статычным высілкам , пры параўнальна невялікай хуткасці працоўнага ходу - 0,1 - 0,3 м/сек.
Па выглядзе энергіі , якая прыводзіць у рух падальныя часткі, молаты падзяляюцца на паравыя і прывадныя (з электрапрывадам). Паравыя молаты без адмысловых пераробак могуць працаваць і на сціснутым паветры, таму іх часта завуць парапаветранымі молатамі. Прывадныя молаты падзяляюцца на пнеўматычныя, з індывідуальным кампрэсарам, убудаваным у станіну молата, рысорныя і рычажныя. З іх найбольшую прымяненне маюць пнеўматычныя молаты.
Па прынцыпе дзеяння пары або сціснутага паветра на поршань.адрозніваюць молаты простага і падвойнага дзеяння. У молатах простага дзеяння ціск пары (або паветра) на поршань знізу выкарыстоўваецца толькі для ўздыму падальных частак уверх. Падзенне іх уніз адбываецца толькі пад дзеяннем сілы цяжару. У молатах падвойнага дзеяння пар (паветра) паступае і ў верхнюю частку цыліндру молата, над поршнем, пры руху падальных частак уніз. У гэтым выпадку яны атрымліваюць дадатковыя паскарэнне і хуткасці, і, такім чынам, молат падвойнага дзеяння развівае большую сілу ўдару, чым молат простага дзеянні, пры той жа масе падальных частак.
Па канструкцыі станіныпарапаветраныя молаты падзяляюцца на аднастойкія, для лягчэйшых прац, з масай падальных частак ад 0,25 да 1 т і двухстоечныя з масай падальных частак ад 1 да 8 т. Найболей зручнымі для кавання буйных фасонных паковак з'яўляюцца цяжкія маставыя трох- васьмітонныя молаты, якія забяспечваюць магчымасць падыходу да байкоў з усіх бакоў.
Прылада і прынцып дзеяння парапаветранага двухстоечнага молата паказаны на мал. IV.22.
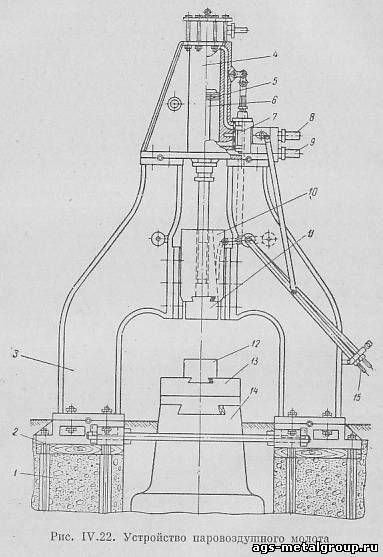
Да бетоннага падмурка 1 праз эластычную пракладку з дубовых дошак 2, змякчальную дзеянне ўдараў, мацуюцца падмуркавымі нітамі стойкі станіны 3. Да верхняй часткі стоек на нітах мацуецца подцилиндровая пліта, адлітая разам з цыліндрам 4. Усярэдзіне цыліндру можа перасоўвацца пад дзеяннем пару або паветра поршень , злучаны са штоком 6, да якога прымацавана баба 10, якая з'яўляецца асноўным элементам падальных частак молата. Верхні баек 11 мацуецца да бабы молата пасродкам злучэння тыпу ластаўчына хваста і сталёвага кліну. Такім чынам, што падалі часткі молата складаюцца з поршня, штока, бабы і верхняга байка. Сумарная маса падальных частак і характарызуе магутнасць молата.
Дэфармаваная ўдарамі верхняга байка нарыхтоўка ўсталёўваецца на ніжнім нерухомым байку 12. Апошні праз пераходную падушку 13 мацуецца да масіўнага шаботу 14, які ўсталёўваецца на пракладцы з дубовых брусоў на бетонным падмурку.
Свежая пара паступае па пароўпускной трубе 8 праз цыліндрычны залатнік 7 у крывалінейныя каналы ў адліўцы цыліндру.
Перасоўванне залатніка пасродкам сістэмы рычагоў ад дзяржальні кіравання 15 дазваляе накіроўваць пар напераменку ў верхнюю і ніжнюю паражніны цыліндру (над поршнем і пад поршнем).
Пры націску машыністам молата дзяржальні ўніз залатнік 7 молата паднімаецца ўгару і тады свежая пара па верхнім крывалінейным канале ў сценцы цыліндру паступае ў верхнюю паражніну цыліндру, душыць на поршань зверху і выклікае паскораны рух падальных частак уніз. Пры гэтым адпрацаваная пара з ніжняй паражніны цыліндру праз ніжні крывалінейны канал у сценцы адліўкі цыліндру выходзіць пад залатніком у паравых лапную трубу 9.
Пры ўздыме дзяржальні кіравання 15 уверх залатнік 7 перамяшчаецца ўніз. Свежая пара, паступаючы з пароўпускной трубы 8, абыходзіць сярэднюю частку залатніка, якая мае меншы дыяметр, і паступае пад поршань у ніжнюю паражніну цыліндру па ніжнім канале ў сценцы цыліндру. Ціск пару на поршань знізу выклікае ўздым яго разам з бабай молата ўверх. Адпрацаваная пара пры гэтым выходзіць праз верхні крывалінейны канал, праходзіць зверху ўніз скрозь полы залатнік і паступае ў паравых лапную трубу 9.
У верхняй частцы цыліндру мацуецца ахоўны буфер, папераджальны ўдар поршня ў вечка цыліндру пры празмерным запаўненні свежай парай ніжняй паражніны цыліндру. Пар ціскам у 7 - 9 ат (0,7 - 0,9 Мпа) паступае да молатаў па трубаправодзе з цэнтральнай кацельні. Калі молат працуе на сціснутым паветры, то апошні падаецца па трубаправодзе ад кампрэсарнай станцыі.
Магутнасць молата выбіраюць у залежнасці ад вагі і складанасці формы пакоўкі. Так, напрыклад, на паўтонным молаце можна адкаваць фасоннае пакаванне масай да 25 кг або гладкі вал масай да 100 кг, а на пяцітонным - фасоннае пакаванне масай да 700 кг або гладкі вал масай 1500 кг.
Пнеўматычныя (прывадныя) молатыз масай падальных частак 75 - 1000 кг шырока ўжываюцца ў кавальскіх цэхах і рамонтных майстэрняў для кавання невялікіх паковак і для штампоўкі ў падкладных штампах.
Пнеўматычны молат мае два вертыкальных раўналежна размешчаных цыліндру - працоўны, у якім ходзіць поршань складнік адно цэлае з бабай, і кампрэсарны. Поршань кампрэсарнага цыліндру прыводзіцца ў зваротна-паступальны рух шатуном ад кривошипного вала, які атрымлівае кручэнне ад электрарухавіка праз рэдуктар. Усе часткі молата змантаваны на літой пустотелой станіне.
Пры руху поршня кампрэсара адбываецца напераменку сціск паветра ў ніжняй і верхняй паражнінах кампрэсарнага цыліндру. Сціснутае паветра праз размеркавальныя каналы і паваротныя краны напераменку паступае ў верхнюю і ніжнюю паражніны працоўнага цыліндру. У выніку пры кручэнні кривошипного вала поршань-баба молата бесперапынна рухаецца ўверх і ўніз, наносячы аўтаматычныя ўдары па пакоўцы. Наяўная сістэма кіравання забяспечвае працу молата і па астатніх цыклах: адзінкавыя ўдары, прыціск пакоўкі, утрыманне байка на вазе і т. д. Сіла ўдару рэгулюецца націскам на дзяржальню кіравання.
Гідраўлічныя ковочные прэсы ўжываюць для кавання буйных паковак.
У гідраўлічную прэсавую ўстаноўку ўваходзяць: уласна прэс; механізм, сілкавальны прэс вадкасцю высокага ціску (прывад); прылады, якія сілкуюць прэс вадкасцю нізкага ціску (рэзервуары-напаўняльнікі). У якасці працоўнай вадкасці ў ковочных прэсах ужываецца вада з растворам у ёй 2 - 3 % эмульсола, які складаецца з мінеральнага алею, алеінавай кіслаты і з'едлівага натра.
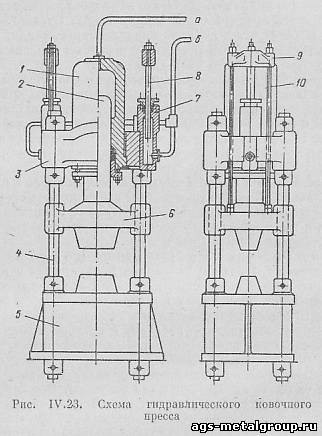
Схема чатырохкалоннага гідраўлічнага ковачнага прэса прыведзена на мал. IV.23. У ніжняй папярочцы (пліце) прэса 5, усталяванай на бетонным падмурку, замацаваныя пры дапамозе масіўных гаек чатыры калоны 4. Гэтыя калоны звязваюць ніжнюю папярочку з верхняй (архітравам) 3, утворачы цвёрдую станіну прэса. Дыяметр гэтых калон у магутных прэсаў дасягае 1 м, а вышыня - 25 м. У верхняй папярочцы замацаваны галоўны працоўны цыліндр прэса 1, у які ўваходзіць галоўны плунжер 2, злучаны з рухомай папярочкай (траверсай) 6, да якой мацуецца верхні баек. Ніжні баек замацаваны ў ніжняй пліце прэса 5.
Халасты ход траверсы з байком уніз да судотыку са зліткам ажыццяўляецца пры паступленні ў галоўны цыліндр вадкасці нізкага ціску з напаўняльнага бака. Напаўняльныя бакі бываюць зачыненыя, вадкасць у якіх знаходзіцца пад ціскам сціснутага паветра ў 4 - 8 кг/см² (0,4 - 0,8 Мпа), або адчыненыя, усталёўваныя вышэй узроўня працоўнага цыліндру прэса.
Працоўны ход ажыццяўляецца пры падачы вадкасці пад высокім ціскам у 200 - 500 кг/см² (20 - 50 Мпа) у галоўны цыліндр прэса па трубе а. Пры гэтым адбываецца рух плунжера з траверсай уніз па накіроўвалых калонах 4 і ажыццяўляецца дэфармацыя злітка, які ляжыць на ніжнім байку.
Зваротны ход - уздым траверсы з верхнім байком пасля працоўнага ходу ажыццяўляецца двума зваротнымі (пад'ёмнымі) цыліндрамі 7, замацаванымі ў верхняй папярочцы. Пры зваротным ходзе вадкасць пад ціскам (або пара ў парогидравлических прэсах) паступае па трубе бы ў ніжнюю частку пад'ёмных цыліндраў, душыць на пад'ёмныя плунжары 8 і прымушае іх паднімаць траверсу 6 пасродкам цяг 10 і папярочкі 9.
Вадкасць высокага ціску падаецца альбо помпай ці помпай- акумулятарнай усталёўкай (чыста гідраўлічныя прэсы), альбо адмысловым памножальнікам ціску - паравым мультыплікатарам (парагідраўлічныя прэсы).
Помпа - акумулятарны прывад забяспечвае найбольшыя велічыню і хуткасць працоўных хадоў прэса, якая дасягае 0,5 м/сек.
Мультыплікаторны прывадмае меншы к. п. д., але забяспечвае большую колькасць хадоў прэса ў хвіліну (да 60) пры невялікіх абцісканнях на аздабленні паковак (шліхтовачныя хады) і дапускае атрыманне значных працоўных намаганняў на байцы прэса за кошт прымянення больш высокіх ціскаў працоўнай вадкасці (400 - 500 кг/см²) (40 - 50 Мпа).
Гідраўлічныя прэсы працуюць без удараў і страсенняў глебы, намаганні, якія развіваюцца імі, успрымаюцца калонамі і не перадаюцца на падмурак. Таму для іх не патрэбен шабат і масіўны падмурак, як у цяжкіх молатаў.
Аднастойкавыя ковочные прэсы для кавання невялікіх паковак складанай формы выпускаюцца намаганнем у 300 і 600 т (2,94 і 5,9 МН). Чатырохкалоннай прэсы для буйных паковак будуюцца намаганнем 500 - 15000 т (4,9 - 147 МН).
Магутныя ковочные прэсы маюць два-тры працоўных цыліндру і могуць працаваць з рознымі намаганнямі пры дзеянні аднаго, двух ці трох цыліндраў.
На прэсе намаганнем у 1000 т (9,81 МН) можна каваць зліткі масай да 8 т, а на прэсе намаганнем у 15 000 т (147 МН) - зліткі масай да 350 т. Пры параўнанні магутнасці молата і прэса прымаюць 1 т масы падальных частак молата прыкладна эквівалентнай 100 т (0,981 МН) намаганні прэса.
§ 19. Тэхналогія кавання тыпавых паковак
Тэхналагічны працэс свабоднага кавання складаецца з падбору нарыхтоўкі і падрыхтоўкі яе да кавання, нагрэву металу, уласна кавання на молаце або прэсе для надання нарыхтоўцы зададзенай формы і памераў і, нарэшце, аздабленні і кантролю пакоўкі.
Пры серыйнай вытворчасці паковак на заводах распрацоўваюцца тэхналагічныя карты, у якіх фіксуецца ўся паслядоўнасць працэсу выраба пакоўкі па аперацыях і пераходам кавання. Да тэхналагічнай карце прыкладваецца чарцёж пакоўкі.
Ніжэй прыводзяцца тэхналагічныя працэсы кавання двух тыпавых паковак: вала з фланцам і шасцярні.
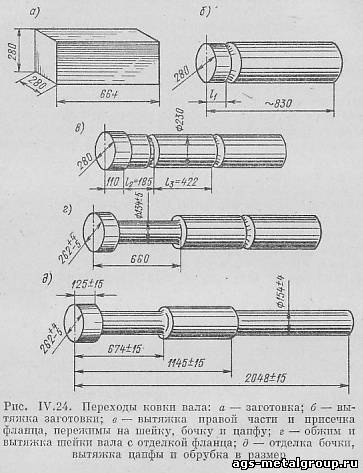
Коўка вала з фланцам. Пакоўка вала масай 382 кг са сталі 45 вырабляецца на молаце 3 т з нарыхтоўкі даўжынёй 664 мм, перасекам 280 х 280 мм.
Нарыхтоўка (мал. IV.24,а), адрэзаная кіслародным разаком, награваецца ў камернай печы да 1200' З і падаецца на баек молата кансольным кранам з падвесным кантавальнікам.
За першы пераход (мал. IV.24,б) нарыхтоўка пракоўваецца па дыяганалях квадрата і працягваецца на дыяметр 280 мм (некалькі большы дыяметра фланца), бо пры наступным пераціску на фланец непазбежная ўцяжка металу ў кутах. За другі пераходвыконваецца пераціск металу вуглавым перацісканнем з выкружкай на даўжыні прысечкі l₁, якая вызначаецца дзяленнем аб'ёму металу, які ідзе на ўтварэнне фланца, на плошчу сячэння F₁ загатоўкі дыяметрам d₁ = 280 мм:

За трэці пераход правая частка загатоўкі (мал. IV.24,в) працягваецца на дыяметр d₂ = 230 мм, некалькі большы дыяметр бочкі вала D₂ = 216 мм, з улікам уцяжкі металу пры наступным пераціску металу на шыйку і правую цапфу вала.
У чацвёртым пераходзе выконваецца пераціск на даўжынях прысечкі:
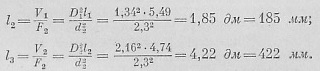
За пяты пераход абціскаецца шыйка вала, спачатку раскочваннямі і на плоскіх байках, а затым у абцісканнях дыяметрам 135 мм у памер па эскізе (мал. IV.24, г). Аздабляецца па дыяметры фланец да паковочного памеру. Пасля гэтага правая частка пакоўкі закладваецца ў печ для падагрэву да 950' С. Невысокі падагрэў, дастатковы для заканчэння кавання вала, папярэджвае рост зерняў металу, у амаль начыста адкаванай бочцы і гатовай левай частцы вала.
У шостым пераходзе працягваецца да канчатковых памераў бочка вала ў абцісканнях дыяметрам 215 мм.
У апошнім пераходзе(мал. IV.24, д) абціскаецца на байках цапфа вала, аздабляецца ў абцісканнях дыяметрам 155 мм і адсякае канцавы адыход. Коўка заканчваецца пры 800 'С. Пасля праверкі памераў і якасці кавання пакоўка накіроўваецца на ўчастак тэрмічнай апрацоўкі для нармалізацыі: нагрэву ў печы да 850 - 870'З з наступным астуджэннем на паветры. Мэта нармалізацыі - драбненне структуры металу і падвышэнне механічных уласцівасцяў пакоўкі.
§ 20. Механізацыя ковочных работ і тэхніка-эканамічныя паказчыкі кавання
Для механізацыі працаёмкіх і цяжкіх аперацый кавання буйных паковак на молатах і гідраўлічных прэсах ужываюць маніпулятары .
Маніпулятар, або «механічны каваль» забяспечаны магутнымі механізаванымі абцугамі, якімі заціскаецца адзін канец нарыхтоўкі ці злітка масай да 30 т. Паварочваючыся адносна сваёй восі, абцугі могуць прыўздымацца і перамяшчацца ў розных кірунках. Маніпулятар можа перамяшчацца па рэйках ці па падлозе цэха. Гэта дазваляе кавалю без працы ажыццяўляць усе патрэбныя змены становішча пакоўкі.
Акрамя маніпулятара пры каванні буйных паковак выкарыстоўваюцца адмысловыя маставыя краны, абсталяваныя падвеснымі кантавальнікамі для падачы і паварочванні зліткаў масай да 200-300 т.
Гідраўлічныя прэсы забяспечваюцца высоўнымі сталамі, якія палягчаюць падачу і выдаленне зліткаў, змену бой.
У апошнія гады на шэрагу заводаў укаранёна аўтаматызацыя кіравання ковачнымі гідраўлічнымі прэсамі і абслуговымі іх маніпулятарамі. Пры гэтым выкарыстоўваецца. сачыльная прылада СШТ-11, якое забяспечвае аўтаматычнае кіраванне прэсам з дапамогай радыёактыўных ізатопаў. Паспяховая эксплуатацыя гэтай прылады на Неўскім машынабудаўнічым заводзе ім. В. І. Леніна забяспечыла паляпшэнне ўмоў цяжкай працы машыніста прэса, павышэнне дакладнасці кавання ў два-тры разы, зніжэнне агульнай працаёмкасці вырабу дэталяў з павышэннем прадукцыйнасці прэса на 15-30%.
Нашы вучоныя і вытворцы працуюць цяпер над вырашэннем задач далейшай аўтаматызацыі тэхналагічных працэсаў кавання і хуткаснай распрацоўкі тэхналагічных карт з прымяненнем электронна-вылічальных машын, а канструктары - над стварэннем кавальскіх машын з праграмным кіраваннем.
Тэхніка-эканамічныя паказчыкі кавання характарызуюцца наступнымі дадзенымі. Выпуск паковак з 1 т масы падальных частак молата складае 200 - 400 кг/ч, з 1000 т ціску гідраўлічнага прэса 2,5 - 4 т/ч. Вынахад прыдатнага металу, вызначаны стаўленнем масы партыі гатовых паковак да масы зыходных нарыхтовак, пры вырабе паковак з гатункавага пракату на молатах складае ў сярэднім 90 - 94%, а пры каванні са зліткаў пад прэсамі - 62 - 66%.
Каэфіцыент вагавой дакладнасці паковак k аў = Gд /G пк (дзе G д - вага дэталі, G пк - вага пакоўкі), які характарызуе тэхнічную культуру вытворчасці, знаходзіцца ў сярэднім пры вольным каванні ў межах 0,40 - 0,50. Такім чынам, аб'ём металу, які здымаецца рэзаннем, складае 150 - 100% ад вагі гатовай дэталі.
|